When a company produces 150 tons of food waste every day that is either a huge problem or a great opportunity to innovate and produce energy.
Kroger’s food divisions, Ralphs and Food 4 Less, opted for the latter. Recently the food would get trucked to a distribution center in Compton, CA, where it was combined and sent to a composter 100 miles away. But now Kroger’s food waste, which was a cost in terms of lost revenue, disposal fees and emissions, is providing cheap, clean energy for the distribution center.
Ralphs and Food 4 Less installed an “anaerobic digestion” system designed by Feed Resource Recovery at the DC: it takes in the food and puts out biogas, providing power for the campus where the center is located. “Anything that can't be sold or donated comes into the system,” said Kendra Doyel, a spokesperson for Ralphs and Food 4 Less, who was quoted in a GreenBiz article.
The digestion system, under development for four years, allows Kroger to turn a waste stream into an energy resource for the 49-acre campus, which includes a creamery and corporate offices for Ralphs and Food 4 Less, along with the 650,000-square-foot distribution center.
Founded in Boston, Mass. in 2007, Feed Resource Recovery designed and implemented a Zero Waste solution for the food industry. It says: “In nature, wetlands use anaerobic digestion to purify the earth’s wastewater. Feed utilizes this natural process, along with proprietary technology and optimization advancements, to cleanly and efficiently convert the carbon in organic waste into a renewable natural gas.”
As described in a Feed Resource video, this is what the system does for Kroger’s Compton campus:
- Powers its facilities
- Produces biogas, augmenting natural gas consumption by 95 percent
- Supplies 20 percent of electricity at the campus
- Captures unused energy from heat
- Heats and re-purposes waste water
- Purifies water
- Produces nutrient-rich organic fertilizers
Here’s the technical part: the process starts when food is brought to the center and put through a blending system that removes any inorganic material such as packaging, such as plastic, metal and glass, and liquefies the food. What's left is organic material that's mixed with wastewater from the creamery.
That mixture goes into an anaerobic digester, an oxygen-free piece of equipment full of microbes that break the food down, producing biogas and a mix of nutrients and minerals. The biogas is then compressed and purified on its way to the campus' microturbines and boilers, where it takes the place of nearly all of the natural gas that the center previously used. The biogas has delivered an 18 percent return on investment for the project so far.
In addition to pulling energy out of waste, the system eliminates a large chunk of truck traffic. Over the past 10 years, the center was sending food waste to a Bakersfield composter in multiple truckloads every day. Kroger estimates that the system will help avoid about 500,000 miles of diesel truck trips a year, saving money that used to pay contractors to move the waste around.
Kroger is Feed Resource’s first client to implement this type of system. With the success at Compton it’s likely that other supermarkets and non-grocery will jump on board.
It’s reminiscent of the old bumper sticker: Eat More Beans: America Needs the Gas!
[Image: Food waste at Kroger's Compton facility via Feed Resource website]
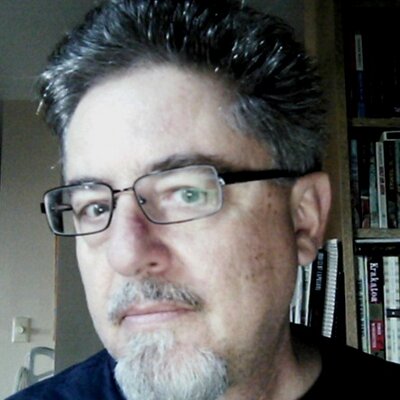
Writer, editor, reader and generally good (okay mostly good, well sometimes good) guy trying to get by.