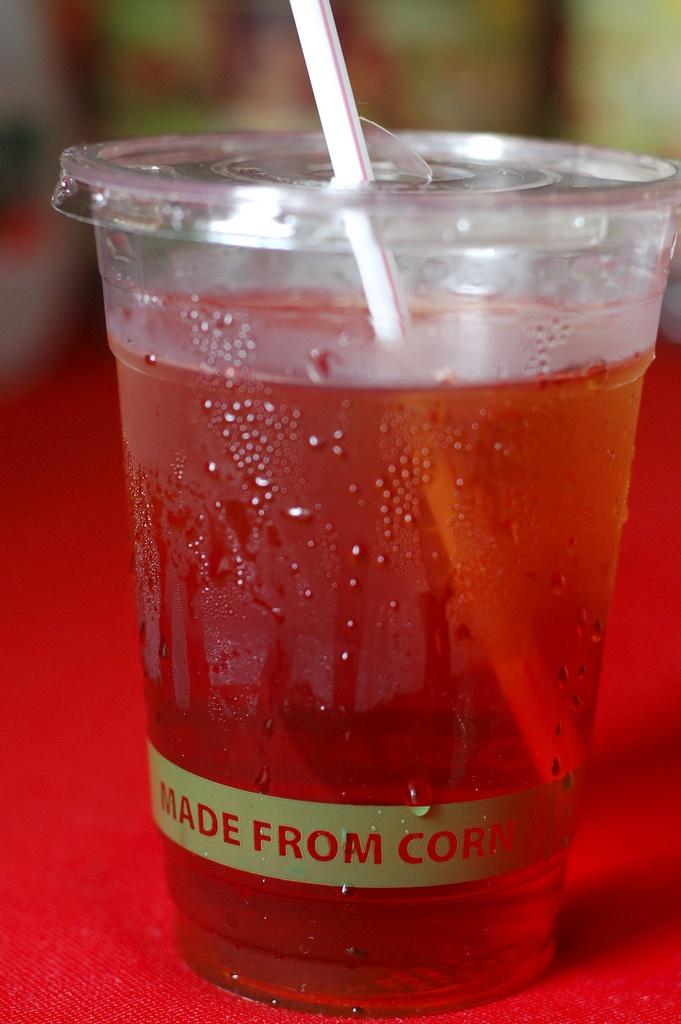
Editor’s Note: This post is part of an ongoing student blogging series entitled The Business Of Sports & Sustainability. This “micro-blog” is the product of the nations first MBA/MPA certificate program dedicated to sustainability in the sports industry. You can follow the series here.
By Jocelynn Stone
It’s the second inning and the Giants have just taken the lead in the NLDS series, the scoreboard has a message encouraging fans to help with recycling and composting in the stadium. Happy that my team is winning, I pick up an empty cup to lend a hand. Confusion sets in. The side of the cup boasts that it is made from plants and on the bottom is the iconic chasing arrow symbol with a number 7 in the middle. Unfortunately, it doesn’t say it is compostable. Should the cup go in the compost bin or the recycling bin?
There are an ever-increasing variety of plastics products derived from renewable raw materials entering the market. The market for biobased and compostable plastics, known as bioplastics, is expected to be worth over $5 billion by 2018 according to Dr. Molly Morse of Mango Materials, a startup that is making biodegradable plastic with methane eating bacteria.
Bioplastics hold great promise. The potential benefits include reducing dependence on fossil fuels and increased diversion of waste from landfills. Readily noticeable is their use in food service items. They are the darlings of sports venues, such as Seattle’s Safeco Field, Yankee Stadium and Penn State’s Beaver Stadium that are working on zero waste initiatives.
Unfortunately, bioplastics may present problems when it comes time to dispose of them.
Not all biobased plastics will biodegrade and not all biodegradable plastics will compost. Many biobased products are designed to behave like traditional petroleum-based plastics and remain structurally intact for hundreds of years. Polyethylene Terephthalate/PET and Polyethylene/PE plastics are being offered in biobased versions. These materials are chemically identical to their petroleum-based cousins and interchangeable in the recycle stream. One example is Braskem’s fully biobased polyethylene.
There is debate about the danger of bioplastics products contaminating the petroleum-based plastics’ recycle stream. It appears that only plastics, biobased or petroleum-based, with identical molecular structures can be recycled together. Likewise, if non-compostable bioplastics make it into the compost stream they cause contamination there.
Compostable plastics, as defined by American Society for Testing & Materials, ASTM D6400, must meet three criteria. They must biodegrade, disintegrate and have no eco-toxicity within 180 days. They require specific conditions in which to decompose and their rate of biodegradation is slower than food and green waste. This requires their being processed at commercial compost facilities.
During a recent visit to the Jepson Prairie Organics composting facility near Vacaville, California we discussed some of the issues posed for their operation by the compostable plastics they receive. They have to separate them from the other compostable waste because their primary compost product is certified organic. Since the majority of bioplastics on the market today are made with GMO feedstock, they don’t fit the criteria for organic certification. Furthermore, because they take twice as long as average to decompose, they have to be processed separately, essentially causing a loss for the facility.
There are three compostable biobased plastic resins that dominate the market.
Polylactic Acid or PLA plastic resin is made by fermenting dextrose from various sources, such as corn, to form lactic acid. This acid is then treated to create lactide and then the final process creates the polymer from which the plastic is made. Natureworks, LLC, a subsidiary of Cargill, uses cornstarch in this process to create their PLA under the brand name Ingeo.
Polyhydroxy Fatty Acids or PHA plastic resin is made from the anaerobic digestion of starch. Basically, a proprietary strain of microbes digest starch and create plastic polymer within their cells, this polymer is then harvested through the destruction of the bacteria. Metabolix makes a bioplastic product called Mirel using this process.
Thermoplastic Starch resin is derived from blending plant based materials, such as starch, vegetable oils and cellulose that have been processed with heat to weaken their polymer structure, with other biobased and/or petroleum-based plastic polymers. An example of Thermoplastic is the product Mater-Bi produced by Novamont.
It turns out my ballpark cup is made of Ingeo PLA resin. It has the chasing arrow symbol #7 because this is the designation for all “other” plastics. Although this plastic is designed to meet the ASTM 6400 standards and biodegrade within 180 days, it is also highly recyclable. Yes, it is both commercially compostable and recyclable. The resin can be remanufactured using less energy than was used to make the original polymer. Ideally, PLA would be separated from the waste stream and recycled for new product instead of being composted.
It would appear that there needs to be clearer marking conventions to aide in proper disposal of these products for recycling or composting. More important, however, is the caveat, that in selecting a bioplastic product for a major application, such as a sports venue, the availability of local composting or recycling facilities for that type of product should be determined before making a material-use selection. As more and more applications for bioplastics products are developed, the feasibility of properly disposing of them should improve.
Photo: Creative Commons, Flicker
Jocelynn Stone designs and manages projects with sustainability in mind. She has a MBA in Sustainable Management from Presidio Graduate School, a BA in Architecture from UC Berkeley and is a Certified Sustainable Building Advisor.
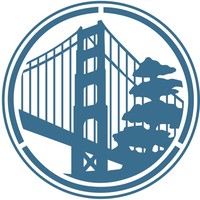
This “micro-blog” is the product of the nations first MBA/MPA certificate program dedicated to sustainability in the sports industry. Led by Dr. Allen Hershkowitz, Senior Scientist at NRDC, The Business of Sports and Sustainability certificate is housed at Presidio Graduate School, the nation’s top sustainable MBA program. Posts explore the connection of sustainability with operations, branding and fan engagement of the sports industry including leagues, teams, venues, sponsors, vendors and surrounding communities.