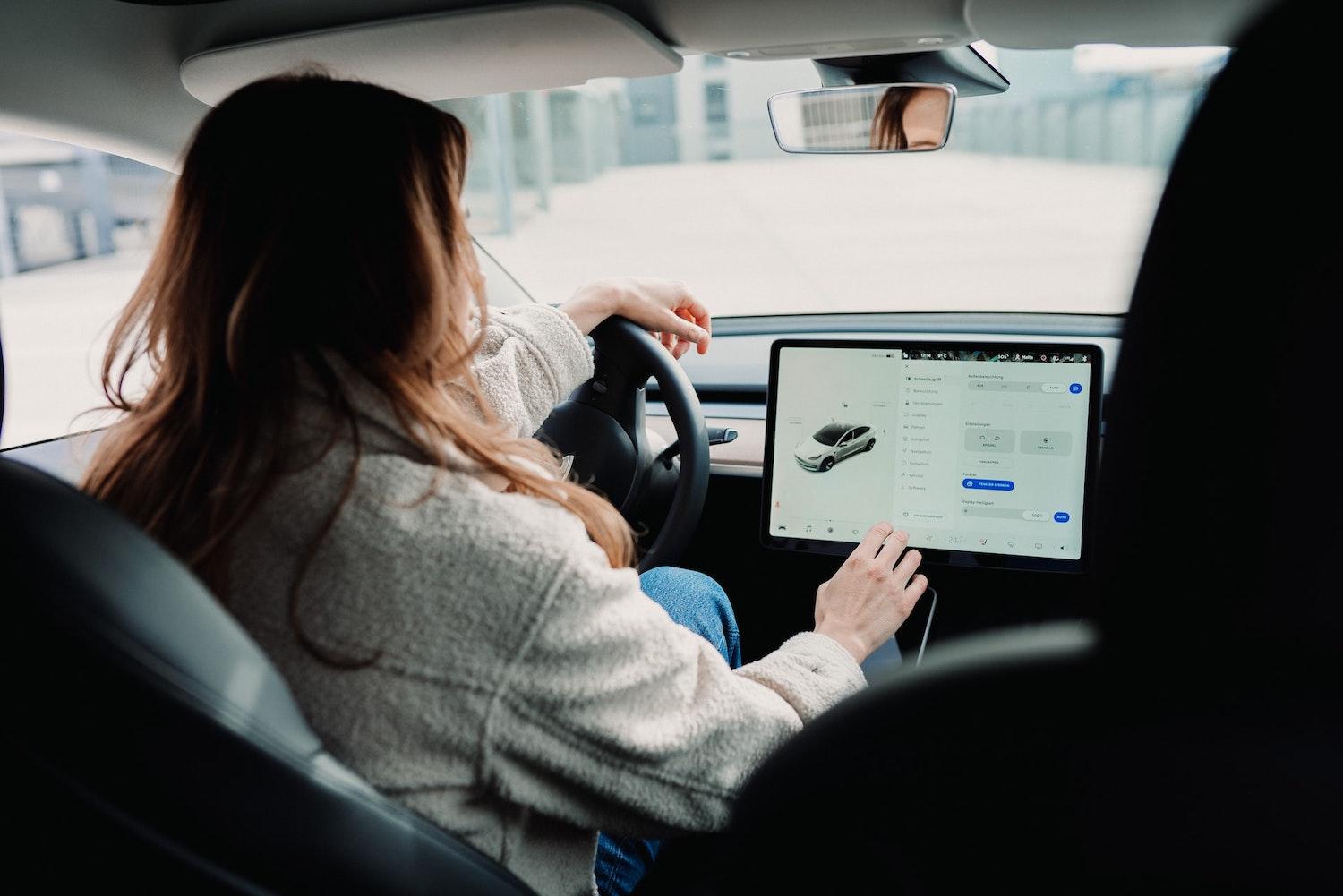
It's hard to argue against the notion that electric vehicles (EVs) are the future of the automobile. By 2035, both the European Union and California have said they will cease to allow the sale of cars powered by the internal combustion engine. Meanwhile, China, a country which already accounts for half of all global EV sales, has crossed the threshold where 25 percent of new car sales are electric.
Looking ahead, demand for EVs is only going to increase. But even at the current level of EV production, the auto industry is already facing some very real supply chain constraints that it will have to overcome in order to scale up the necessary battery production. To convert the world's auto fleet to EVs is going to need some serious innovation.
During the BNEF Summit in San Francisco last week — a meeting of the minds focused on the convergence of transport, energy and technology — the state of play for EV battery technologies was addressed in depth, and it's a tale of both challenge and opportunity.
The challenge: Battery costs are on the rise again amidst strained materials supply
Here's the challenge: Although EVs are still more expensive to produce than comparable internal combustion engine (ICE) cars, over the last decade, the burgeoning EV market has coincided with the steady fall in EV battery cost. Until recently, it seemed we were close to seeing battery costs falling to $100 per kilowatt-hour — the holy grail that will enable EVs to reach price parity with ICE-powered cars.
Unfortunately, that downward cost trend has now reversed. That's because the price of battery materials have started to increase due to constrained supplies of lithium, cobalt, manganese and nickel. As a result, batteries won't reach the $100-per-kWh level until 2026, said Evelina Stoikou of BloombergNEF, two years later than the research provider previously predicted.
Consequently, at least in the short term, automakers are scrambling to shore up supplies. This is manifesting in aggressive hedging within the industry to partner with raw materials suppliers, Stoikou said at the event. And beyond forging partnerships, some automakers are investigating vertical integration, such that some might even take ownership of certain raw materials mining.
As a result, the industry is already in somewhat of an arms race just to meet today's needs. But, going forward, these supply constraints will drive innovation. In order to realize a global fleet of EVs, batteries will need to come to market which reduce or eliminate certain components that are difficult to source reliably, responsibly and affordably.
U.S. startups explore new battery technologies for a low-carbon future
In a panel discussion at the BNEF Summit, representatives from U.S. battery startup companies discussed how the country can deliver competitive batteries in the future against this backdrop of fierce competition.
Today, China holds the competitive advantage. Batteries made there are already 24 percent cheaper than those made in North America. This is aided by the fact that China is a major supplier of lithium globally, while battery technologies there benefit from strong policy support by the Chinese government and robust investment in the activity.
Of course, when we talk about EV batteries today, we are talking about lithium-ion batteries. All pure EVs on the road in America today are powered by them. The dominant lithium-ion chemistry in the U.S. is specifically lithium-ion NMC, so called because these batteries use nickel, manganese and cobalt (NMC) in their cell cathodes.
The industry has generally settled on lithium-ion NMC batteries because they deliver a superior energy density necessary for the vehicle ranges customers demand today.
These batteries have given us cars with 300 or more miles per charge. But panelist Celina Mikolajczak, chief battery technology officer for the California-based startup Lyten, asserted that if we seek a world with electrification for everyone, lithium-ion NMC is not going to get us there — pointing out there's just not enough nickel out there.
Lyten instead focuses on a lithium-sulfur technology, which Mikolajczak readily admits is a challenging chemistry to settle upon. Both sulfur and lithium are each unruly elements on their own, let alone in combination. But Mikolajczak and Lyten believe it's worth the effort as sulfur is abundant and cheap, while the chemistry offers good energy density and rapid charging capabilities.
Though Lyten's focus is lithium-sulfur, it's just one of a range of alternatives.
An established chemistry that is already becoming more important today is lithium-ion LFP, which replaces nickel and cobalt with iron and phosphorus in the battery cell cathode. A key benefit of LFP batteries is that, again, certain scarce elements are replaced by more abundant and less expensive ones. Iron and phosphorus are easy to get ahold of and don't depend on foreign supply. LFP batteries are also longer lasting, able to sustain more charge cycles than NMC batteries and are less susceptible to thermal runaway (and in turn, fire, which is always a good thing).
Pros and cons: Balancing tradeoffs in emerging battery technologies
Perhaps predictably, though, there's always a catch with the alternatives. For example, lithium-sulfur batteries suffer from the corrosive nature of sulfur, making these batteries traditionally short lived. LFP batteries, on the other hand, are less energy dense and heavier than NMC batteries, meaning they generally achieve shorter driving ranges.
This is not to say these impediments cannot be overcome. Rather, it illustrates that battery technologies are still firmly in the innovation and iteration stage.
Panelist Deanna Ahmed, VP of strategy, policy and sustainability at Michigan-based Our Next Energy (ONE), agrees that nickel and cobalt have to be minimized going forward. ONE's battery also incorporates LFP chemistry as a part of its “Gemini” architecture. However, the company's solution is a dual-chemistry battery which combines an anode-free cell that acts as a power reserve, feeding a LFP traction battery to propel the vehicle. In a proof-of-concept demonstration, ONE retrofitted a Tesla Model S with its Gemini battery, allowing it to travel 752 miles on a single charge. ONE believes EVs need to get double the range typically achieved today in order for customers to be truly past their range anxiety.
There's agreement, then, that eliminating cobalt and nickel are priority steps — especially as these elements are often sourced from politically problematic places. But eliminating lithium is another innovation that could potentially remove yet another supply-constrained element.
Natron Energy is working on a sodium-ion platform that eliminates mineral supply constraints altogether. CEO and co-founder Colin Wessells estimates the technology could be as energy dense as LFP batteries in 15 to 20 years. But this technology is unlikely to power vehicles any time soon: The chemistry is currently focused on static energy storage — and as we will need more energy storage as more renewables come online, it could be an important part of the battery mix as well.
Which tech is best?
Of course, it's dodgy territory picking future winners when it comes to emergent battery technologies. There have been lots of lofty promises made about new battery chemistries developed in laboratories that never seem to manifest successfully in the field.
But to pick one that's already gaining the most ground, you probably have to go with the aforementioned lithium-ion LFP batteries, at least in the short term.
Already, Tesla is using lithium-ion LFP batteries for its standard-range vehicles while it uses lithium-ion NMC batteries for performance- or extended-range cars that need the extra oomph. As EV drive trains become more efficient, decent range can be maintained with smaller and less energy-dense batteries. Additionally, smaller urban-focused EVs prevalent in some global markets see LFP batteries already dominating.
And perhaps very importantly, and to tie this into the U.S. Inflation Reduction Act (IRA), avoiding nickel and cobalt means LFP batteries can be produced using more North American-sourced materials. A requirement for benefits available through the IRA places limits on the amount of foreign-sourced materials that are allowed.
Further, the IRA could be a boon to U.S. battery technologies and innovators going forward. The panelists at BNEF agreed that the legislation will be useful for companies with proven technology to go to scale, due to the investment tax credits available. It's one thing figuring out a battery technology, and another to figure out production methodology at scale and start opening giga-factories. The IRA could help bridge that divide.
Also, available investment in battery technologies and manufacturing could help develop a domestic battery manufacturing workforce of skilled blue-collar occupations — which, as Lyten's Mikolajczak says, are the kind of blue-collar jobs we want in the country.
Image credits: Jenny Ueberberg and Precious Madubuike via Unsplash
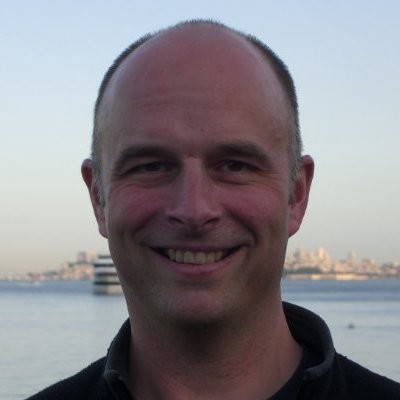
Phil Covington holds an MBA in Sustainable Management from Presidio Graduate School. In the past, he spent 16 years in the freight transportation and logistics industry. Today, Phil's writing focuses on transportation, forestry, technology and matters of sustainability in business.