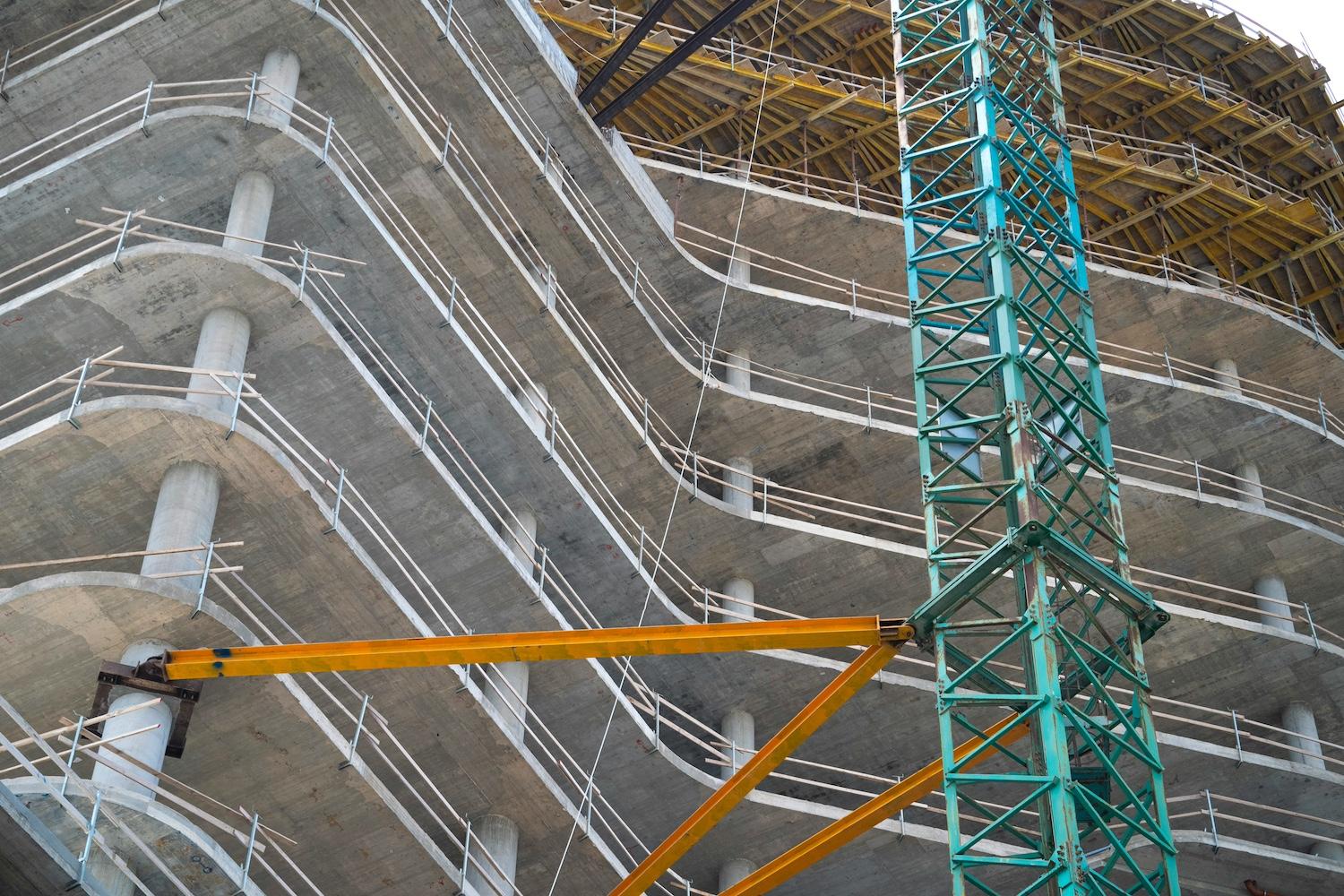
(Image: Evan Demicoli/Unsplash)
The workaday world of concrete is getting a long-overdue makeover, as new lower-carbon mixes enter the market. But with millions of possible mixes already available, choosing the most sustainable concrete for a project is all the more complicated. If that sounds like a job for artificial intelligence (AI), it is.
The U.S.-based startup Concrete.ai has developed an AI-powered platform that helps project managers sort through the options and find the optimal mix for the job, with both sustainability and performance as key factors.
Building our way into catastrophic climate change
Concrete accounts for about 9 percent of all greenhouse gas emissions. All else being equal, that figure is all but certain to expand in the coming years, fueled by urbanization, industrialization and population growth.
The technological obstacles to decarbonizing concrete have been formidable. Over the past 10 years, other sectors of the global economy made significant strides in adopting renewable energy, electric vehicles, and other pathways to a low-carbon economy. In contrast, new processes for making concrete were slow to emerge.
The main obstacle is cement, which is the binder that mixes with water, sand, gravel and other fillers to form solid concrete. Cement only accounts for about 10 percent of the total mix, but it’s the main source of greenhouse gas emissions from concrete production. Making cement involves both fossil energy and a chemical reaction that releases carbon dioxide.
Cement is made of a material called clinker, which is processed from clay and limestone. “Limestone … is baked at up to 1,450 degrees Celsius (2,640 degrees Fahrenheit) in enormous kilns that are fired almost exclusively with fossil fuels,” Scientific American reports. “The chemical reactions involved produce even more carbon dioxide as a by-product.”
Those chemical reactions have not changed since cement was first invented more than 200 years ago, as Isabel Malsang wrote for Phys.org. “If concrete were a country, it would be the third largest emitter of greenhouse gases on Earth, behind only China and the United States,” Malsang notes.
Building our way out of catastrophic climate change
Fortunately, new approaches are emerging. One avenue is the “buildings as material banks” concept, which supports a circular economy model that can help reduce greenhouse gas emissions through recycling and reuse. New building materials like cross-laminated timber can also help reduce the use of concrete.
New technologies that directly reduce carbon emissions from cement and concrete making are also appearing. In January, the U.S. Department of Energy selected five firms to share a total of $20 million in funding for new cement and concrete technologies aimed at reducing greenhouse gas emissions.
One of the awardees, the Massachusetts startup Sublime Systems, received a $6.7 million grant to develop a process that deploys renewable energy and electrification to replace combustible fuels. The company also uses non-limestone feedstocks to produce its low-carbon cement.
AI helps to choose the right concrete mix for the job
Another approach is illustrated by the California firm CalPortland, which received a $4 million grant to develop a method for reusing the cementitious materials in waste concrete. The company also recovers stone and other aggregate materials for reuse.
As these new materials come on the market, either as drop-in replacements or feedstocks for blending, building project managers will be faced with an even more complicated array of choices to make.
TriplePundit spoke with Alex Hall, CEO of the U.S. startup Concrete.ai, to learn more about the scope of the challenges involved in selecting the most optimal concrete mix for columns, floors, pavements and other infrastructure.
“Concrete … is the second most consumed product after water,” Hall said. “Just in the U.S., we produce 15 million cubic yards per year. We pour enough concrete every 3.5 days to build another Hoover Dam.”
There are 6,000 ready-mix concrete plants in the U.S. alone, Hall told us. As a group, they deploy 10 to 25 different materials to offer a range of mixes covering over 2,000 different designs. All together, the number of possible concrete mixes reaches into the millions.
New, lower-carbon cement provides the opportunity to introduce sustainability as an optimizing factor, without impacting performance. However, introducing new mix designs is typically a long, slow process of trial and error. That is the obstacle tackled by Concrete.ai’s signature product, Concrete Copilot.
“Historically the way we’ve built these designs is through experimentation, looking at end results, validating the process. This is slow and iterative,” Hall said. “Now we apply our patented models to these elements. Ultimately it’s about data. The more data we have about the performance, then we can start the validation process.”
How it works: The benefits of data
Concrete Copilot uses an AI platform created over a 10-year period at the Institute for Carbon Management at the University of California, Los Angeles. Based on criteria submitted by concrete producers, the platform can generate millions of possible mix designs in a matter of seconds and present the most optimal design. The producer can accept the mix as-is or modify it according to their needs.
In addition to evaluating their current formulas, producers can use Concrete Copilot to evaluate new products and respond quickly to shifts in their supply chains.
Concrete.ai launched the platform commercially in January following a period of extensive field testing among concrete producers across the U.S. last year, covering more than 2 million cubic yards of concrete.
“The average material savings were $5.04 per cubic yard, and the average carbon reduction was 30 percent,” the company reported. “For most producers, these results were seen within just one month of activating the platform.”
The potential for rapid transformation
The leading U.S. concrete firm VCNA Prairie Material provides a good example of the potential for a rapid transformation of the concrete industry.
Chris Rapp, vice president and general manager of VCNA, told 3p that the last “revolutionary” change in the concrete industry happened about 15 years ago when paperless, electronic delivery ticketing began.
“Innovation happens very slowly in our industry,” he said. “Ready-mix is still very archaic.”
Nevertheless, VCNA is on the alert for new opportunities to innovate. The company participated in the field tests for the AI solution last year, providing VCNA's team with about five months of experience using mixes generated by Concrete Copilot by the time it launched commercially.
“From a client perspective, there is little difference in what they’ve seen in the past,” Rapp said. “They get a mix design with a lower carbon footprint but the performance is the same.”
Rapp also anticipates that new alternatives to cement will be widely accepted, though the sheer volume of the industry presents a hurdle to scale up. “Anything that can replace cement that doesn’t sacrifice performance is the way this market will trend eventually,” he said.
In the meantime, cement stakeholders that seek to gain an edge on decarbonization can take steps now, as illustrated by the leading firm Holcim. The company has introduced a lower-carbon concrete that incorporates alternative materials, including recovered demolition debris.
Last October, Holcim announced a $100 million upgrade for its cement plant in Ste. Genevieve, Missouri. When it’s completed in 2025, the upgrade will increase the capacity of the facility — which is already the largest facility of its kind in North America — by 600,000 metric tons while reducing net carbon dioxide emissions by more than 400,000 tons.
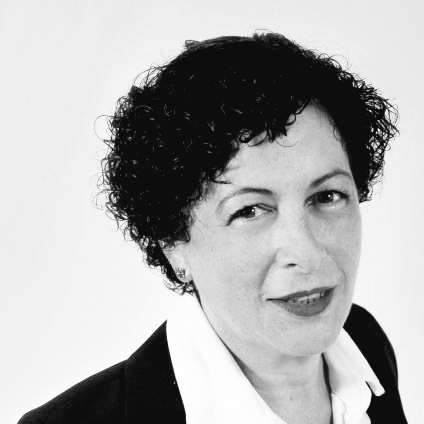
Tina writes frequently for TriplePundit and other websites, with a focus on military, government and corporate sustainability, clean tech research and emerging energy technologies. She is a former Deputy Director of Public Affairs of the New York City Department of Environmental Protection, and author of books and articles on recycling and other conservation themes.