Waste heat recovery has emerged as an effective way of increasing energy efficiency at factories where refrigeration is crucial. Any energy savings is important because even though commonly used refrigerants such as hydrofluorocarbons (HFCs) do not deplete the ozone level as chlorofluorocarbons (CFCs) did a generation ago, HFCs still pose global warming potential (GWP). A combination of using refrigeration gases with no GWP, plus more efficient heating and cooling systems, can save companies hundreds of thousands of dollars with one factory retrofit alone.
Food processing plants can especially benefit from such an upgrade. Conventional refrigeration compressors require huge amounts of energy to keep chocolate both molten and cooled, fruits and vegetables fresh and, of course, factory workers comfortable. But the heat generated from a compressor’s activity has long been emitted into the atmosphere. A simple change in technology, however, can make these compressors more powerful and efficient, and therefore able to divert that once-wasted heat for additional uses. During my recent telephone conversation with Emerson Climate Technologies’ Business Director, Sam Gladis, he explained how the company’s technology benefits companies and municipalities.
Most refrigeration compressors use a traditional male-female rotor alignment to compress gas. While this ensures a smooth operation and seamless processing of gases, there is a limit to how much pressure such a system can handle. Refrigerants such as ammonia are one option for companies to consider, both for its efficiency and the fact it does not contribute to ozone depletion or greenhouse gas emissions. But, for demanding industrial heating and cooling applications, plant managers had shunned ammonia because no compression pumps could handle this refrigerant at high pressure levels. According to Gladis, refrigeration technology really had not changed much in 150 years, with the result that no process had existed to convert heat released by compressors into other heating or cooling uses.
The solution was a single screw compressor system the company Vilter had developed during the 1980s. The mechanism looks simple: it is simply one main main rotor that intermeshes with two gate rotors on both sides. Eventually, one of the company’s consultants informed Vilter’s management that the compressor’s design actually allowed gases to be processed at very high pressures--and higher differential pressure ranges--while offering low life-cycle costs. Because of the single screw’s compressor-balanced design, a factory also benefits from lower maintenance and operational costs because of their decreased strain on the compressor’s bearings.
One company that is benefiting from Vilter’s technology (Emerson purchased Vilter in 2009), is Nestlé. One of its factories in the United Kingdom was the first project to implement Vilter’s compressors. A coal-fired plant had powered the chocolate factory in the town of Halifax, but Nestlé’s managers wished to upgrade to a system that could trap waste heat from refrigerating chocolate . . . and then convert it in order to shape chocolate products elsewhere in the factory.
The new Vilter system, launched in May 2010, has shown a 15 percent higher energy efficiency rate than the previous system. The factory has reduced its CO2 reduction by 1.1 million pounds annually. And on the ledger, the new compressors and waste heat recovery system saves Nestlé almost $400,000 in energy costs a year.
Municipalities can also save money by installing a waste heat recovery system. District heating is a common method to deliver heating to communities in Europe. The system involves one centralized cogeneration plant instead of a less efficient system of localized boilers. Drammen, a town of 60,000 near Oslo, Norway, has turned to the North Sea as a clean energy source to heat its buildings. Water in the nearby North Sea can dip as low as 43°F, but a proper heat pump can extract heat from it.
The catch is a system rigorous enough to process a refrigerant while keeping maintenance costs low. Drammen officials worked with Emerson to install heat pumps that could handle a refrigeration system running ammonia. That frigid water can reach a temperature of 194°F and, in turn, help keep Drammen’s businesses and residents warm during Norway’s frigid winters. “It is the largest such project that has ever been done and reaches the highest temperature using ammonia,” said Gladis as we wrapped up our talk.
Heat recovery systems like that of Vilter’s are an example of how smart retrofits can decrease both a company’s impact on the environment as well as operating costs. Such an investment is also a solid first step in boosting energy efficiency if renewable technologies such as solar or wind are not an option either because of the local climate or regulatory environment.
[Image credit: Vilter/Emerson]
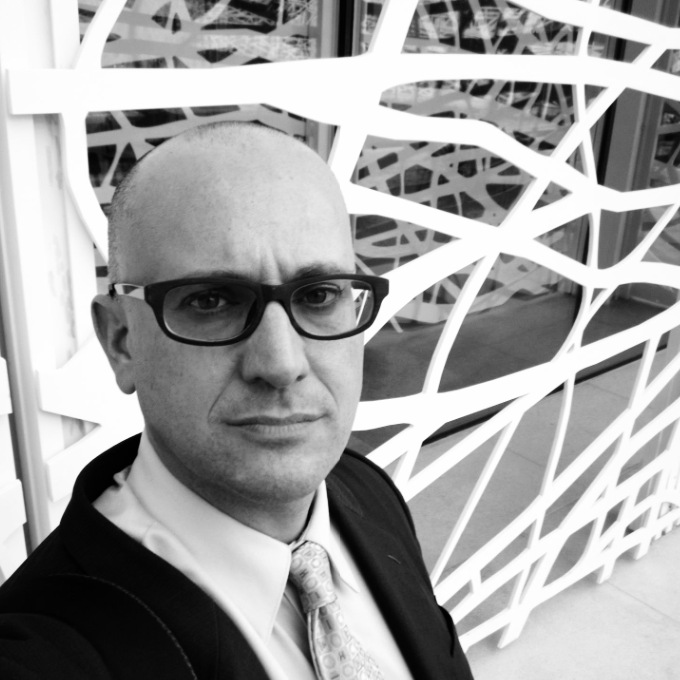
Leon Kaye has written for 3p since 2010 and become executive editor in 2018. His previous work includes writing for the Guardian as well as other online and print publications. In addition, he's worked in sales executive roles within technology and financial research companies, as well as for a public relations firm, for which he consulted with one of the globe’s leading sustainability initiatives. Currently living in Central California, he’s traveled to 70-plus countries and has lived and worked in South Korea, the United Arab Emirates and Uruguay.
Leon’s an alum of Fresno State, the University of Maryland, Baltimore County and the University of Southern California's Marshall Business School. He enjoys traveling abroad as well as exploring California’s Central Coast and the Sierra Nevadas.