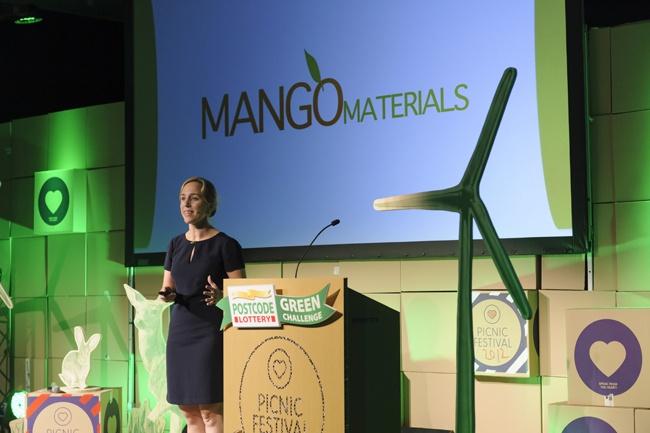
Ed note: This is a sponsored post on behalf of the Postcode Lottery Green Challenge
Plastics are a thorn in the side of environmentalists: The ubiquitous material is made from nonrenewable resources like oil, may leach chemicals over its lifetime, isn’t always easily recyclable and takes thousands of years to degrade in the landfill. But Molly Morse thinks she has come up with an environmentally responsible alternative: a bio-based plastic that is made from waste methane gas and can be recycled over and over again.
The environmental engineer and CEO of Mango Materials won the 2012 Postcode Lottery’s Green Challenge, one of the world’s preeminent sustainable business plan competitions. This is the eighth year the challenge is inviting entrepreneurs and startups from the U.S. and other countries to enter for a chance to win €500,000 ($680,000) to help bring their green products and services to the mass market. An additional €200,000 ($272,000) will be awarded to one or two runners-up. The deadline to apply is June 3 via www.greenchallenge.info.
The feedstock for Morse’s innovative eco-plastic is waste methane gas from wastewater treatment plants, landfills and agricultural facilities. Classified as a greenhouse gas that contributes to global warming, methane is potentially 20 times more potent than carbon dioxide and also plays a role in the depletion of the ozone layer. Morse and her team at Mango Materials use bacteria to transform methane into pellets or powder of a biodegradable, bio-based polymer – poly-hydroxybutryate (PHB) – that has similar properties to polypropylene and can be made into a variety of products, including electronic casings, children’s toys, shampoo bottles and packaging.
When the PHB products reach the end of their useful life, they can be sent to a landfill or digester, where they degrade and produce methane – which can be made back into PHB plastic. How quickly the product biodegrades depends on the landfill environment and the material’s thickness, the California-based startup said on its website.
“…The process can be a completely closed loop, cradle-to-cradle solution with a significant impact on the worldwide plastics market,” Morse wrote on a Huffington Post blog. “And, by providing an incentive for methane capture, it will promote the sequestration of millions of pounds of this greenhouse gas.”
PHB is cost-competitive with conventional petroleum-based plastics and cheaper to produce than bio-plastics made from plants, according to Morse. To keep transportation costs down and lower the product’s environmental footprint, Mango Materials can co-locate with waste methane producers and pipe the gas directly into the company’s plant.
Morse said she was always concerned about plastic waste.
“I'm the kind of person who flinches at the use of disposable plastic silverware,” she wrote on the Huffington Post. “I have been known to scold people who answer ‘yes’ when the grocery clerk asks if they want a bag, and I regularly rescue plastic bottles from trash cans for recycling.”
Working with the Engineers for a Sustainable World in India after the 2004 tsunami, Morse saw temporary shelters made from plastic used fleetingly and then thrown away. This experience motivated her to explore sustainable, biodegradable alternatives to plastic in the lab at Stanford University when she was pursuing her masters and doctorate degrees in civil and environmental engineering.
Since winning the Green Challenge in 2012, Mango Materials has hired new team members, bought new equipment and supplies, and formed new partnerships, Morse wrote in the Green Challenge blog. The startup also received a $500,000 Phase II award from the National Science Foundation, which it used to scale up and complete the company’s first bio-plastic production run in August 2013 in its new, larger lab space with its new bioreactor system. Morse’s team is currently producing research-grade materials only, but aims to have trial samples available soon.
Think you have what it takes to win the Postcode Lottery’s Green Challenge?
If you have an idea for a product or service that reduces greenhouse gas emissions and is ready to enter the mass market within two years, consider applying for the Postcode Lottery’s Green Challenge. You’ll need to submit a detailed business plan and elevator pitch by midnight (central Europe time) on June 3. Learn more details about the competition here.
“Winning the Green Challenge will always be a special memory for me,” Morse wrote on the competition's blog. “It was the moment when I knew we finally had the opportunity to really tackle the challenge of global warming and plastics in the environment. The days are still long, but they are full of purpose and passion.”
Image credit: Postcode Lottery Green Challenge
Passionate about both writing and sustainability, Alexis Petru is freelance journalist based in the San Francisco Bay Area whose work has appeared on Earth911, Huffington Post and Patch.com. Prior to working as a writer, she coordinated environmental programs for Bay Area cities and counties. Connect with Alexis on Twitter at @alexispetru
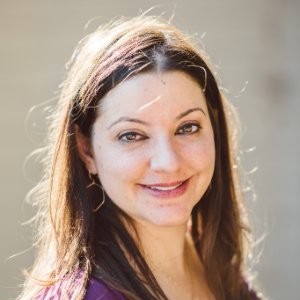
Passionate about both writing and sustainability, Alexis Petru is freelance journalist and communications consultant based in the San Francisco Bay Area whose work has appeared on Earth911, Huffington Post and Patch.com. Prior to working as a writer, she coordinated environmental programs for various Bay Area cities and counties for seven years. She has a degree in cultural anthropology from UC Berkeley.