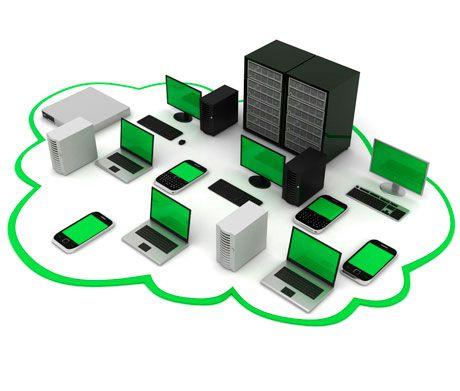
Some of the world's largest multinational businesses have recognized the advantages 'closing the loop' on their supply chains can provide. From energy and water conservation to materials reuse and recycling, they're achieving significant gains in operating efficiency and productivity as they move toward becoming 'zero-waste' and 'zero emissions' businesses.
Mimicking natural ecosystems, commercial and industrial ecosystems are emerging -- in which an increasing percentage of products, their components, and raw or intermediate materials are being reused or recycled. The ultimate goal -- cradle-to-cradle product lifecycles in which all materials used to produce, package and distribute products to consumers are recaptured, reused or recycled -- is edging closer to reality.
At the leading edge of this movement is a small group of companies operating in what has come to be known as reverse supply chain management. Aiming to close the loop on the supply chain, they're advancing green economy initiatives by offering original equipment manufacturers (OEMs) across a growing range of industries an integrated 'one-stop shop' for re-manufacturing, as well as reusing and recycling products, their constituent parts and raw materials.
Reversing the supply chain
The ever-growing amounts of plastic, metal, chemical and non-biodegradable waste being transported, dumped and accumulating in public and private land and landfills poses serious threats to human and environmental health. While tax-paying residents and businesses around the world are paying for waste hauling, treatment and processing services, OEMs and other businesses all along product supply chains are leaving a lot of money, as well as social and environmental benefits, on the table.
By enabling them to move beyond conventional concepts of reuse and recycling, reverse supply chain manufacturers can help companies capture that value, comply with environmental regulations, and enhance the legitimacy and credibility of their sustainability strategies.
Offering post-consumer takeback and recycling, enterprise IT and telecom asset management, and 3R solutions for mobile devices, Hong Kong-based Li Tong Group owns and operates 15 reverse supply chain facilities worldwide. From an OEM customer base in the consumer electronics sector, Li Tong is intent on expanding its reverse supply chain business across other industry sectors, Linda Li, a Li Tong executive director and corporate VP for strategy, told 3p in an interview.
Li Tong is providing reverse supply chain services to some of Silicon Valley and the tech industry's biggest companies. It's now expanding across the telecommunications sector, where network equipment and device manufacturers, as well as cloud service providers, are looking to 'green' their businesses.
Growing waste consciousness
Until recently, what happens to a product once it's disposed hasn't been an issue given much consideration by businesses or governments. That's changed dramatically over the course of recent decades as the environmental and human health and safety threats of what we throw away have been better understood and more widely recognized. This growing consciousness has given rise to the “cradle to cradle” movement, a term coined by architect and sustainability advocate William McDonogh and German chemist Michael Braungart.
“When I talk about reverse supply chain management, I talk about all that can be done after a product is in a consumer's hands,” Li explained. That includes taking back "defective products, returns, fulfilling warranty agreements, repairs, refurbishing, disposal, reuse and recycling." Now part and parcel of a growing number of CE OEM's operations, “consumer take-back schemes are just one aspect of this.”
At present, large amounts of waste are built-in to product life cycles. When it comes to supply chain management, “forecasting is never very accurate,” Li continued. “Let's say a manufacturer builds in a 10 percent buffer to accommodate projected demand for a product – they expect to sell 100 million units, but they manufacture 110 million just in case actual exceeds their forecast.”
Those buffer amounts ripple across the supply chain. “Everyone builds in a buffer – no one wants to run short – we call it the 'bullwhip effect,'” Li elaborated.
The Bullwhip Effect
Indicative of how the 'bullwhip effect' amplifies the magnitude of materials waste across the supply chain, “Three to five percent of annual CE shipment volume is deemed obsolete and needs to be scrapped before it is ever even used to produce a consumer electronics product,” she pointed out.
The bullwhip effect is particularly strong in the CE industry, where short product life cycles are the norm. “For every 100 million smartphones shipped, 3 to 5 million will be set for the scrap heap,” Li told 3p.
“New CE product lines and models may be introduced every six months. That makes massive waste a reality of the high-tech industry. What happens to all this material has a huge environmental impact, as well as lots in the way of lost economic value.”
Conventional waste management and recycling companies typically wind up leaving a lot of value unrealized, Li said. Li Tong enables OEMs and supply chain partners to capture a much higher percentage of their inherent value as compared to companies that offer scrap, recycling and waste management services, she continued.
The people it employs are the key element of its ability to deliver on these promises. Capturing the value from waste CE and high-tech products requires a lot of specialized knowledge, as well as processes and other resources, Li pointed out. "Our engineers all come from an electronics manufacturing background...When it's 'first life' is finished, we can take CE and other high-tech products apart and harvest their components and parts – from an LCD, a Wi-Fi module, a memory storage device, a CPU,” she elaborated.
“There's no reason they need to be decomposed to fragrments. Whole parts or components can be reused – the LCD in a mobile phone or tablet, for example, might be reused to make a GPS handset or smart home appliance.”
The Internet of Things is already beginning to open a wide variety of new opportunities to reuse and recycle parts and components from electronic devices and equipment.
“Think of the carbon footprint, the environmental impacts, then the economic value that can be recovered,” Li said. “That's the solution we are offering all our OEM customers – reuse, re-manufacture and recovery are the three 'R's' upon which our business is built.”
*Image credits: 1), 3) Li Tong Group; 2) Reverse Logistics Association
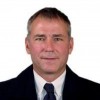
An experienced, independent journalist, editor and researcher, Andrew has crisscrossed the globe while reporting on sustainability, corporate social responsibility, social and environmental entrepreneurship, renewable energy, energy efficiency and clean technology. He studied geology at CU, Boulder, has an MBA in finance from Pace University, and completed a certificate program in international governance for biodiversity at UN University in Japan.