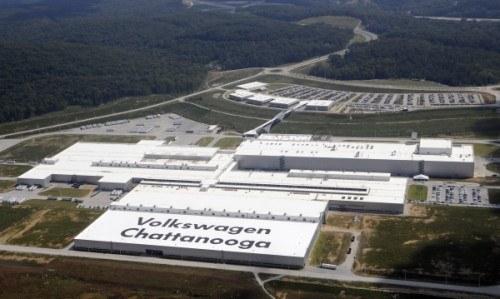
Volkswagen’s Chattanooga, Tennessee plant is well known for its accomplishments in environmental sustainability. It claims the record as the world’s first Platinum LEED certified automotive facility, and its 9.5 million watt solar array, cool building strategies and water catchment systems have garnered environmental awards and global recognition. Just as importantly, the plant’s design has proven to industry leaders that sustainable approaches can have a place in high-energy-usage industrial settings.
And green tech isn’t the only place where Volkswagen has been applying its sustainability talents these days. Workforce education plays a critical role in today’s automotive industry, where a robotized production line commands a higher need for specialized training, not less. Automotive positions that interface with that mechanized environment now benefit from a college education and specialized training that goes beyond the manual, front-line labor of previous generations. Today’s workers are in many cases, the essential support network that keeps those robots repaired, wired and working.
But there’s a catch. Getting trained mechatronics personnel who are familiar with VW’s specialized, LEED-compliant operations and who have met the scholastic requirements of an associate degree or above can be a challenge. A two-year degree in automotive mechatronics varies widely in cost in the U.S., ranging from $10,000 for the live-at-home in-state resident, to upwards of $20,000 for the out-of-state student who pays full price and may live off-campus. And that still doesn’t meet the greatest challenge of all: ensuring that newly minted graduates can land on their feet running and adapt to VW’s own specialized way of building cars from the date of hire.
That’s where the dual apprenticeship programs come in. According to Ilker Subasi, who serves as the assistant manager of technical training at VW’s Chattanooga plant, the company’s three-year mechatronics associate degree – the first of its kind in North America – blends the on-the-job training with the classroom curricula of a college-level associate degree program. It gives the Chattanooga College student the ability to link the theoretical with the hands-on application in the factory. And it gives VW a potential roster of trained, skilled professionals to hire.
By housing the apprenticeship program on site, VW is able to tailor its new mechatronics programs – automation mechatronics program and the car mechatronics program – to fit the schedule within the plant, offering the new students an up-close view of the work environment as well as daily hands-on experience.
“It is unique to have an associates degree in a hands-on training program in a company. Basically, they don’t go to the campus of Chattanooga Community College,” said Subasi. “They all stay at the plant and the teachers [come] to us.” The students earn a monthly stipend during the three years of training, and if they pass the final testing, are offered a job upon completion that comes with benefits and a competitive salary.
Automotive apprenticeships are a new concept in the U.S. and gaining attention for their ability to solve a fundamental problem of the 21st century: how to equip unskilled labor for an increasingly technical and changing manufacturing environment. In Germany and other European countries, apprenticeship programs are common and fill a vital niche in the labor market. Here in the States however, the concept of the paid student worker who competes to study and train onsite has fallen off. Only about five percent of workers enroll in apprenticeship programs, compared to a whopping 60 percent in Germany.
But VW representatives admit that launching the first apprenticeship program in Chattanooga took some legwork. Both Tennessee’s State Board of Education and Chattanooga College had to be convinced that a program that integrated a college degree and automotive training and was taught and accredited completely on site would really work.
“We’ve worked hard to get the word out,” admitted Scott Wilson, who is the head of Communications and Public Relations. “It’s really a matter of education. People didn’t understand what it meant.”
But today, with one graduation under its belt and a growing roster of applicants for the two programs, as well as a proven track record in being able to place the students they’ve trained, VW can say that its German apprenticeship program is in fact, transportable, and offers a framework that can be used to fill other educational niches as well.
This year, Chattanooga launched a new apprenticeship program that would integrate the skills of college-educated engineering specialists who already have a Bachelors degree and want to tailor their skills to mechatronics.
“We provide them hands-on comprehensive training in 18 months,” explained Subasi. It’s geared toward electrical engineering and machining professionals that may have never worked in an automotive plant, but have the advanced skills that VW needs on its workforce. The first month provides an accelerated introduction to mechatronics. The remaining time is spent in the engineering department. At the end of the 18 months, the student is sent overseas to Germany to experience what it’s like to work in one of VW’s other plants. Like the mechatronics associate-degree programs, the engineering specialist program is accredited through Chattanooga Community College.
Although it is only in its pilot stage, VW expects to have the engineering program will get a good response. Like the mechatronics apprenticeships, it fills a void in today’s vocational job market by helping to merge solid academic training with the needs of a dynamic and increasingly mechanized industry.
And they are helping to transform the U.S. job environment in other ways as well. Enrollees in VW’s apprenticeship programs are encouraged to take training sabbaticals overseas. Mechatronics and engineering students both receive classes in German during the academic portion of the training, making it easier for them to apply for limited assignments in Germany and other parts of the world. The benefit expands their exposure to other languages and broadens their experience in other cultural settings. Subasi said the concept appeals to VW’s global vision.
“It’s part of our global strategy to have flexible workforce development,” said Subasi, who notes that VW has more than 106 plants across the globe. We are really a global player. We have over 560,000 employees worldwide. So we have to be flexible.”
The programs also help to reduce downtime due to unexpected vacancies, since they are cross-trained in a number of areas, said Albert Graser, VW’s technical training specialist in Chattanooga. “Our qualifying students are able to work in a number of areas, so if there’s an issue in electrical mechanical or what have you, these guys are trained to work in all the areas and are pretty self-sufficient.
After more than three years on Chattanooga College’s academic roster, VW’s apprenticeship programs are beginning to garner attention from Washington and Nashville. Wilson said the new programs have driven home the point that “skilled maintenance jobs, skilled manual labor jobs are viable alternatives for people to have a productive career.” And just as importantly, it’s helped to illustrate ways that businesses can – and perhaps should – play a role in shaping the education that will ultimately define their future workforce.
Images courtesy of Volkswagen Group of America
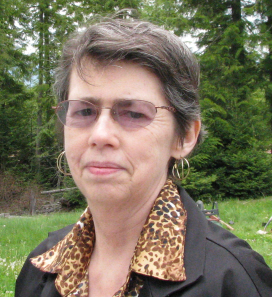
Jan Lee is a former news editor and award-winning editorial writer whose non-fiction and fiction have been published in the U.S., Canada, Mexico, the U.K. and Australia. Her articles and posts can be found on TriplePundit, JustMeans, and her blog, The Multicultural Jew, as well as other publications. She currently splits her residence between the city of Vancouver, British Columbia and the rural farmlands of Idaho.