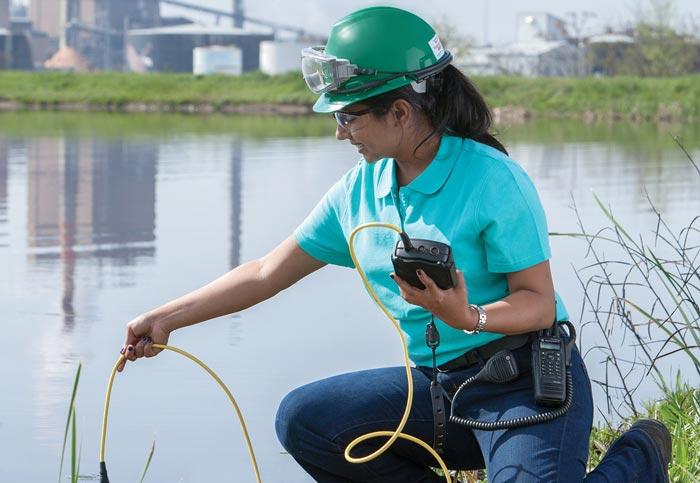
As we study the key systems upon which our human population depends, it quickly becomes clear that water and energy are essential. Not only are they essential, but they are also inextricably linked. It takes energy to move, heat and purify water. It also takes a great deal of water to produce energy, whether it’s from hydropower or from thermal power plants, both nuclear and fossil fuel-fired.
The most prominent example of this interdependency is in agriculture, which uses enormous quantities of both energy and water. The paper industry differs from agriculture for a couple of important reasons. First, 72 percent of the fiber used in paper comes from trees which are rainfall-fed. This, in water conservation parlance, is considered green water -- which is distinguished from surface and groundwater, referred to as blue water. Agriculture also depends on rainfall, but in many cases it is supplemented by a great deal of additional water via irrigation, which is why the industry is by far the largest water consumer in the nation.
Most of the water used in the paper production life cycle is used during the manufacturing process, primarily for conveyance of the fibers as they are extracted from logs as wood chips, and through the pulping process. By the same token, most of the energy used in paper-making goes into cooking the pulp, in order to remove the fibers, and drying the wet fibrous mat as it comes out of the paper machine before it is rolled up and ultimately cut into reams or converted into cardboard. According to this Energy Star report, more than $7 billion worth of energy was purchased in 2009 for the manufacture of pulp, paper and paperboard. This is primarily used as boiler fuel for both process-steam and power generation.
Of course, there is an opportunity to do things in a smarter and greener way. There is a great deal of residual biomass such as bark that could be used to produce energy. International Paper does exactly that, generating 72 percent of its energy from forest residuals. The company has also been working to improve energy efficiency, with a goal of a 15 percent reduction in purchased energy by 2020. An investment of $290 million has led to a reduction of 9 trillion BTUs per year. At current coal prices, that will pay for itself in 8 years, though if natural gas is substituted, it could take longer. Since 2010, the company has reduced its purchased energy usage per ton of paper by 3.7 percent.
Some examples include:
- Eastover Mill in South Carolina leveraged a $21 million investment to reduce energy consumption by 26 percent. This resulted in an elimination of 50,000 tons of coal per year.
- Svetogorsk Mill in Russia launched a new 25-megawatt combined heat and power system (CHP), which generates electricity and process steam at efficiencies significantly higher than standalone power generation. That’s enough for 16,000 U.S. homes, with steam being provided as an essentially free byproduct.
- Maysville, Kentucky Mill invested in paper machine heat recovery, which should save the equivalent of 12,000 tons per year of coal annually. The project takes hot exhaust gas from the paper drying process and uses it for heating water, decreasing the need for fossil fuel.
On the water side of the story, I spoke with Adam Miklos, International Paper’s Business EHS manager, responsible for water, about the company’s progress in this area.
What’s important to understand, when talking about water conservation, is that we’re really talking about conserving available water. Whenever water is used, most of it generally makes its way back into the water supply, locally, through the sewer system. The rest is either removed through evaporation, or is actually bound up in the product. All of that will eventually be returned to the planetary supply, but it is removed from the local water supply and is therefore considered consumed. Of course, any water that is contaminated must be treated before it can be safely used again for all purposes.
Triple Pundit: Can you give us a little background on the role that water plays in the papermaking process?
Adam Miklos: Water is often used to help convey the various materials through the process. We take incoming wood and digest chips until we have fiber in an aqueous solution. Then we wash and bleach the pulp. Ultimately it gets sent into a paper machine where it is laid out on a wire that forms the sheet of paper, which is then dried. So there are various points in the process where we are adding water, extracting water and evaporating water. Additionally, water is used for things like cooling equipment and providing steam.
3p: So where have you found the opportunities to conserve?
AM: Historically, most of the water that was used in the process was fresh water. Either it was extracted from the ground, a river or a public water supply. That fresh water was directly applied to one part of the process, and then it would be considered used, and sent to the water treatment plant. The biggest change, over the past twenty to thirty years, is the internal reuse of that water. So now we take the effluent from one step in the process and use it in another step, depending on the requirements of each step and the quality of the effluent. If the effluent is warm, we try to use it in a process step that needs warm water. If the contaminant level is low, then we direct it to another step in the process where that level is acceptable.
3p: Is that philosophy used throughout the process?
AM: Yes, though it is easiest to see in our washing operations, in a process called counter-current washing, where the cleanest water coming off the last stage is directed to the next cleanest stage and so on. The water is recycled all the way through that process. Some water is used for cooling equipment and even, then circulated through cooling towers, where the heat is removed and the water can then be reused. We only add water to those process to make up for water that has evaporated or water that has to be purged due to contaminant levels.
3p: What kind of reductions has this led to?
AM: Since the 1960s, we have reduced the amount of water required to make a ton of finished product by 50 percent.
3p: Is that on a gross or net water basis?
AM: We look at the total withdrawals. That’s how much water we take into our facility, in total, to make each ton of paper. We also look at how much water we put back into the receiving stream. The difference between those two is what we call our consumptive use.
3p: So how much water is that?
AM: For 2013, we used roughly 46 cubic meters of water per metric ton of production, throughout the enterprise.
3p: Is that the consumptive use or the withdrawal?
AM: That’s the total withdrawal. Consumptive use varies from facility to facility. Typically, it runs between 5 to 7 percent of the total withdrawal. Most of that consumption is the water that has evaporated in the process, either when the paper is dried, or through natural processes as it makes its way through the water treatment system.
3p: So compared with traditional methods, you’re probably withdrawing less than half the amount of water.
AM: That’s correct.
3p: You mentioned a number, which is an average across the enterprise. How much does that vary from mill to mill?
AM: We’re a collection of different types of mills. We’ve got some mills that make brown paper. We’ve got some mills that make recycled paper and some that make bleached paper. There are different levels of water intensity across those different mills. Some of our bleached mills, may, in fact be over a hundred cubic meters per ton, but when you look in totality, our average is around 46.
3p: How does recycled paper factor in?
AM: In some cases, recycled fibers are blended in with virgin fibers to produce finished products. In other cases we are using 100 percent recycled fiber to make our products. When you look at the spectrum of water use in our facilities, mills tend to use more water because they require a number of additional process steps, including, in some cases, an oxygen delignification step. These steps, which essentially convert a brown fiber to a white fiber, require a higher utilization of water. Recycled mills, on the other hand, do not require a wood yard. They do not require a chemical pulping process. What we’re doing in those mills is taking in recycled fiber, breaking it back down to individual fibers and then sending it into the paper machine. They tend to be very efficient in terms of their water usage.
3p: So using recycled paper really helps reduce water consumption.
AM: Yes. But recycled paper has advantages and disadvantages when compared to virgin paper in terms of its strength characteristics and the range of applications that’s its suitable for. But where it’s suitable, it’s a very water efficient product.
3p: Relative to that that 46 cubic meters that you withdraw on average, how does recycled paper compare?
AM: Roughly 10.
3p: That’s quite a difference. Good to know.
AM: We have a number of mills that make varying grades of paper, with different proportions of recycled content. We’re able to do that because we have pulping lines and recycled lines co-located.
3p: So what other areas are you looking into for additional opportunities to reduce water consumption?
AM: We think it’s pretty much an issue of reuse. Many of these processes fundamentally depend on using water. So it’s about figuring out how we can clean it up and use it over again. We are working with some of our chemical vendors to improve the chemical addition process, adding new injection technology so that we can use less dilution water. That helps us save water and energy, since much of that dilution water must be heated. Some paper machines can use clarified white water instead of fresh water, in the machine’s shower water systems. It’s a continual evaluation, looking for opportunities. We think most of the low-hanging fruit has been picked, so now we’re looking higher up in the tree.
3p: What priorities drive your search?
AM: We’re looking at those facilities where our water risk is the highest. So if we’re in an area where there is acute water stress, we’re taking additional steps to align our water use and our water investments with whatever constraints might exist in a given area. Our priority is to minimize our impact and preserve our ability to continue producing paper in those areas. The last thing we want to do is to use water irresponsibly in a water-stressed area.
3p: Can you give me some examples of what you’ve done in water risk areas?
AM: We’ve got a paper mill in Kenitra Morocco. There is very little water there. We’ve reduced our water use within that mill by almost 50 percent since 2010. We did it using technologies that were less common in that region and applying them there. Another example, in Pensacola, Florida, where there are groundwater issues, we are using reclaimed water from the local utility authority to help offset groundwater use.
3p: What are your goals moving forward?
AM: We’re doing a strategic water mapping exercise this year, from which we will determine both the opportunities and specific targets.
Image courtesy of International Paper
RP Siegel, PE, is an author, inventor and consultant. He has written for numerous publications ranging from Huffington Post to Mechanical Engineering. He and Roger Saillant co-wrote the eco-thriller Vapor Trails. RP sees it as his mission to help articulate and clarify the problems and challenges confronting our planet at this time, as well as the steadily emerging list of proposed solutions. His uniquely combined engineering and humanities background help to bring both global perspective and analytical detail to bear on the questions at hand.
Follow RP Siegel on Twitter.
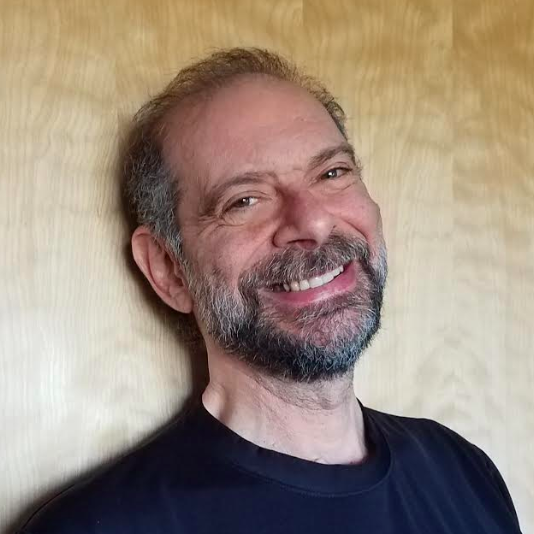
RP Siegel (1952-2021), was an author and inventor who shined a powerful light on numerous environmental and technological topics. His work appeared in TriplePundit, GreenBiz, Justmeans, CSRWire, Sustainable Brands, Grist, Strategy+Business, Mechanical Engineering, Design News, PolicyInnovations, Social Earth, Environmental Science, 3BL Media, ThomasNet, Huffington Post, Eniday, and engineering.com among others . He was the co-author, with Roger Saillant, of Vapor Trails, an adventure novel that shows climate change from a human perspective. RP was a professional engineer - a prolific inventor with 53 patents and President of Rain Mountain LLC a an independent product development group. RP was the winner of the 2015 Abu Dhabi Sustainability Week blogging competition. RP passed away on September 30, 2021. We here at TriplePundit will always be grateful for his insight, wit and hard work.