
It's no secret that one of the world's most pressing problems is discarded plastic. It's everywhere: in landfills, in vast quantities in our recycling bins and in even greater quantities in our oceans.
Although companies like Levi's, the New York Institute of Technology's Home20 and public figures like will.i.am have made great strides in finding uses for things like discarded plastic bottles, we're still faced with more than 3 million tons of plastic in the Pacific Ocean alone and an unfathomable expanse of garbage across our public waterways.
While organizations like the Ocean Cleanup are doing their part to corral this debris, others are working to create ways to put plastic to work. But the sheer volume of plastic waste led some innovators to seek ways to use it in one of today's most popular and increasingly useful designs: 3-D printing.
The concept seems simple: Convert the world's various plastic bottles, containers, bags and other debris into filament that can be fed into personal and industrial 3-D printers. The 3-D technology allows companies to "print" on-the-spot models for architectural design, medical research and manufacturing prototypes. In fact, 3-D printers have become a valuable tool for many types of operations where only a single item is needed, said Dr. Bob Pfahl, a senior consultant for the nonprofit research and development consortium, the International Electronics Manufacturing Initiative.
"In the electronics industry ... the primary use has been in making prototypes of products," Pfahl told TriplePundit. It's also used to construct temporary test molds of metal machinery, like injection molding. Pfahl said the test mold cuts production time, as well as reduces the cost of a prototype. "You can cut down on your production time by about 30 days, maybe more than that."
The technology has also been used by "one of the major automobile firms to make fixturing ... to hold pieces in place so people can assemble [new cars]," Pfahl continued.
Even the military has found a use for 3-D printing: to fill the need for parts that are no longer manufactured. "It is ideal for that, because the cost is not the major issue," Pfahl said. "It is getting the part [that's important]. Those are applications where volume is limited and you get the advantage of these unique and unusual shapes."
3-D printing with plastic waste: It's all in the chemistry
And in recent years, the concept of on-the-spot printing has become an advantage for home hobbyists, entrepreneurs and artists, who have a singular, limited use for a homemade prototype. The newer, transportable 3-D printers are geared for the average person who wants to print (more accurately build) his or her own reproduction in the comfort of a home or office.
So, creating filament out of the miles of plastic trash that's been scooped up from the Pacific Ocean, or dredged out of landfills, is a very tempting idea. It seems like the perfect answer to a uniquely 21st-century headache.
There's one problem, Pfahl said. Actually, there are several.
"Properties will degradate." In other words, the properties that those brightly-colored filaments are made from are critical to the outcome of the 3-D product. Consistency is often the determining factor.
Pfahl used a project that he worked on with Motorola years ago to illustrate the problem. In that case, the task was finding a way in which old compact disks (CDs) could be melted down to make cellular phone cases.
"The first thing we discovered was the weight of [the CD material] was much lower than what was needed" for the cell phone case, Pfahl explained. That meant the polymer wouldn't be strong enough for its intended use and would have to be combined with other substances to make it work. "We could only use up to 18 percent polycarbonate, which was the material we were using, because after that point those properties degenerated."
Dr. Carol Handwerker, who serves as the Reinhardt Schuhmann Jr. professor of materials engineering for Purdue University, explained it another way. When it comes to the integrity of a polymer substance like polyethylene, chemical composition of what you are working with is critical.
"You can have very different [kinds of] polyethylene, depending upon how many repeat units there are in the polymer," Handwerker said.
"Polymers like polyethylene, which is what both flimsy plastic bags and durable detergent bottles are made out of, comprise long hydrocarbon chains. In chemistry terms, the composition and branching of that chain defines the behavior of that particular polymer. Even though the plastic bag and the laundry detergent container are both made of polyethylene, their molecular structure is totally different. So is their behavior when exposed to heat, chemicals and other stresses. Combining multiple kinds of polymers can change the performance of the filament in a 3-D printer.
And so can impurities: additives that may be used to give a product a certain look or make it perform in a special way. In the case of Pfahl's CD example, metal etching served as the frustrating component in the mix. But impurities can be plastics as well, noted Dr. John Howarter, assistant professor in materials engineering at Purdue University.
"So, that would be a mixing in of a second-grade polymer, or maybe a completely different type of polymer," Howarter told us.
And the challenge isn't always a matter of strength, or integrity, he explained. "If you are actually going to use these in electronics, the property called the dialectric constant (which in simple terms, describes the flow of energy through a material) depends on all of these kinds of impurities as well."
These challenges are often unique to polymers, Howarter said. "If we are talking about aluminum, aluminum has the same melting temperature ... Polymers and polyethylene don’t work that way."
If the printer head on the 3-D printer is calibrated to operate at 200 degrees Celsius, and the molecular structure of the recycled plastic material isn't consistent with that demand, "maybe you aren’t going to get a molten polymer that can then be integrated into that 3-D part," he continued. "Any time we are talking about recycling polymers, these are challenges that people in the industry are up against and I think have to be mindful of when they are saying, 'Okay, we’re going to recycle this.'"
Turning challenges to solutions
Pfahl noted that the cost of recycling can often be a consideration as well. "[In] the electronics industry, using recycled materials is very challenging." So is separating smaller pieces of plastics from the discarded product. "The costs of bringing them back for energy may very well outweigh the advantage of recycling those materials."
While there are a few companies that have developed filament out of recycled product, its application is anything but wide-ranging. Howarter speculated that the filament is probably very limited in its use at this point. "And it is also going to be especially formulated for that [model and brand of] machine," he said.
Still, 3-D printing has opened up all kinds of innovations, said Handwerker, who recounted a story about a grandmother who, upon reading about the process in a women's magazine, embarked upon the task of figuring out how to craft hands for her grandson, who had been born without fingers. In fact, the story has been played out multiple times in the private sector, where 3-D printers have not only inspired hopeful answers to global problems, but extraordinary gifts from strangers.
Howarter agreed. "I think where the 3-D market really is, is enabling individuals on a local scale to make products and to make parts that you couldn’t ever convince a billion-dollar industry to customize ... I think that is where you are going to start seeing the presence of 3-D printing, especially when it comes to polymers."
And if plastics scooped up from the Great Garbage Patch have a future in 3-D printing, it will probably be that kind of collective effort and open-source innovation that will make it possible.
Image credits: 1) & 2) Makerbot 3-D printer and BEETHEFIRST printer and filament: Flickr/Creative Tools; 3) Plastic debris at Ocean Beach Calif.: Flickr/Kevin Krejci
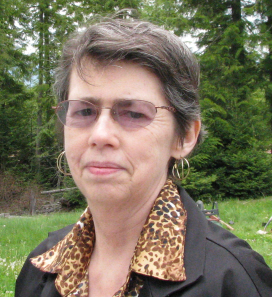
Jan Lee is a former news editor and award-winning editorial writer whose non-fiction and fiction have been published in the U.S., Canada, Mexico, the U.K. and Australia. Her articles and posts can be found on TriplePundit, JustMeans, and her blog, The Multicultural Jew, as well as other publications. She currently splits her residence between the city of Vancouver, British Columbia and the rural farmlands of Idaho.