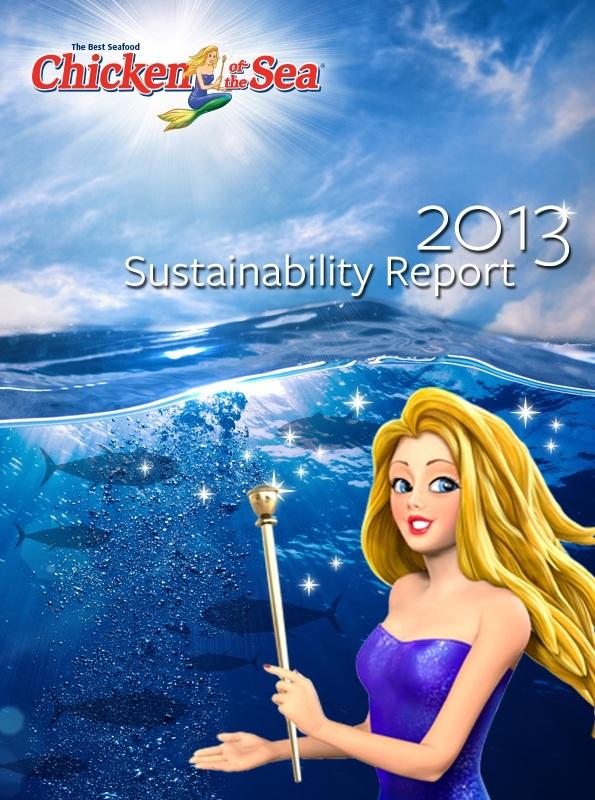
Seafood giant Chicken of the Sea’s latest corporate sustainability report reveals some important milestones the company achieved in 2013. Among the most notable was a 27.8 percent reduction in waste. The company also cut water use by 12.8 percent for every case it packed.
The report documents its efforts, with a focus on “four pillars” of sustainability, and sets goals to be met by 2020.
The four pillars are: employees, facilities, products and suppliers. And goals were set in the following areas: energy, waste, water, health and safety, and supply chain. This is the third year Chicken of the Sea has collected comprehensive data on practices throughout the company and its supply chain.
“Past reports and research have been critical to our understanding of the current and potential global and industry sustainability landscape, and where we stack up in that environment,” said David Roszmann, the seafood giant's chief operating officer and leader of its sustainability initiatives. “This year, we were able to take our work to the next level by adding specific, measurable goals in areas that matter most. Our vision is to be the first consumer choice in seafood, and to get there, a clear sustainability path focused on continuous improvement is critical.”
The company summarized its sustainability goals and the progress it made in 2013:
- 20 percent reduction in electricity and natural gas use (per standard case of product) by 2020: As a result of retrofitting its canning facility for lighting upgrades in high-traffic areas, Chicken of the Sea reduced electricity usage 4.4 percent in 2013, when adjusted for production. The company plans to use a variety of measures to continue to reduce its usage, such as reducing lighting and HVAC in unused areas and during non-production times, installing LED lighting, and working with a consultant to identify additional cost-efficient, energy saving measures for its facilities. Natural gas use increased by 10.2 percent on a production-adjusted basis and is a focus for future efficiency improvements.
- 30 percent reduction in landfill waste (per standard case) by 2020: In 2013, the company recorded a 27.8 percent drop in the amount of waste it takes to produce a case of product. It attributed this to implementing a new recycling program in its production areas and training employees on recycling and waste minimization practices. The company says it will put additional waste reduction initiatives into place this year.
- 15 percent reduction in water use (per standard case) by 2020: The company’s 12.8 percent water reduction was a result of conservation efforts, the reports authors said. These included installing new thaw chambers at its Lyons, Georgia, canning facility in 2012 and limiting in-process water usage, such as monitoring wash-down hoses to prevent wastewater when not in use.
- Maintain or reduce safety incidents by 2020: In 2013, the company saw a 40 percent lower incident rate than the previous year, experienced only six lost workdays and averaged a 2.5 incident rate -- compared to the state of Georgia’s 5.4 average incident rate.
- Audit 90 percent of seafood procurement spend (on a three-year rolling basis) by 2020: The company audited 37 percent of its vendors and suppliers in 2013 as it launched a formal sustainability auditing process. “The third-party audits look at its suppliers’ labor and human rights performance, environmental management systems, and overall business practices.” The company says it will audit additional suppliers each year and re-issue audits every three years.
“Looking ahead, we face very real challenges,” said Shue Wing Chan, Chicken of the Sea's president and CEO. “On the environmental front, we must find better ways to improve our natural gas use, which increased by 10.2 percent on a production-adjusted basis. While we have begun to investigate our options, we must be aggressive at identifying and implementing new technology and behaviors.”
Chan added that the company “must continue to pay close attention to our supply chain impacts … Over the next few years, we will be placing particular attention to working with our parent company and our key suppliers to ensure that labor and human rights are upheld from ocean to table.”
Chan is correct when he says supply chain, human rights and labor issues are an “industry-wide challenge.” And auditing 90 percent of seafood procurement spending is even more ambitious.
Image credit: Chicken of the Sea's 2013 corporate sustainability report cover
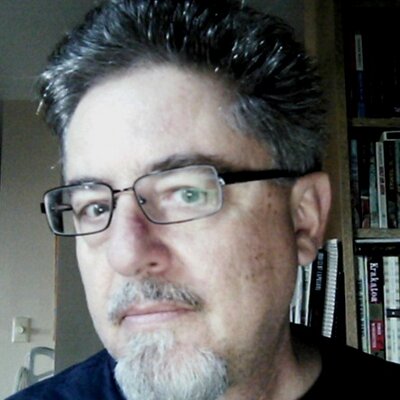
Writer, editor, reader and generally good (okay mostly good, well sometimes good) guy trying to get by.