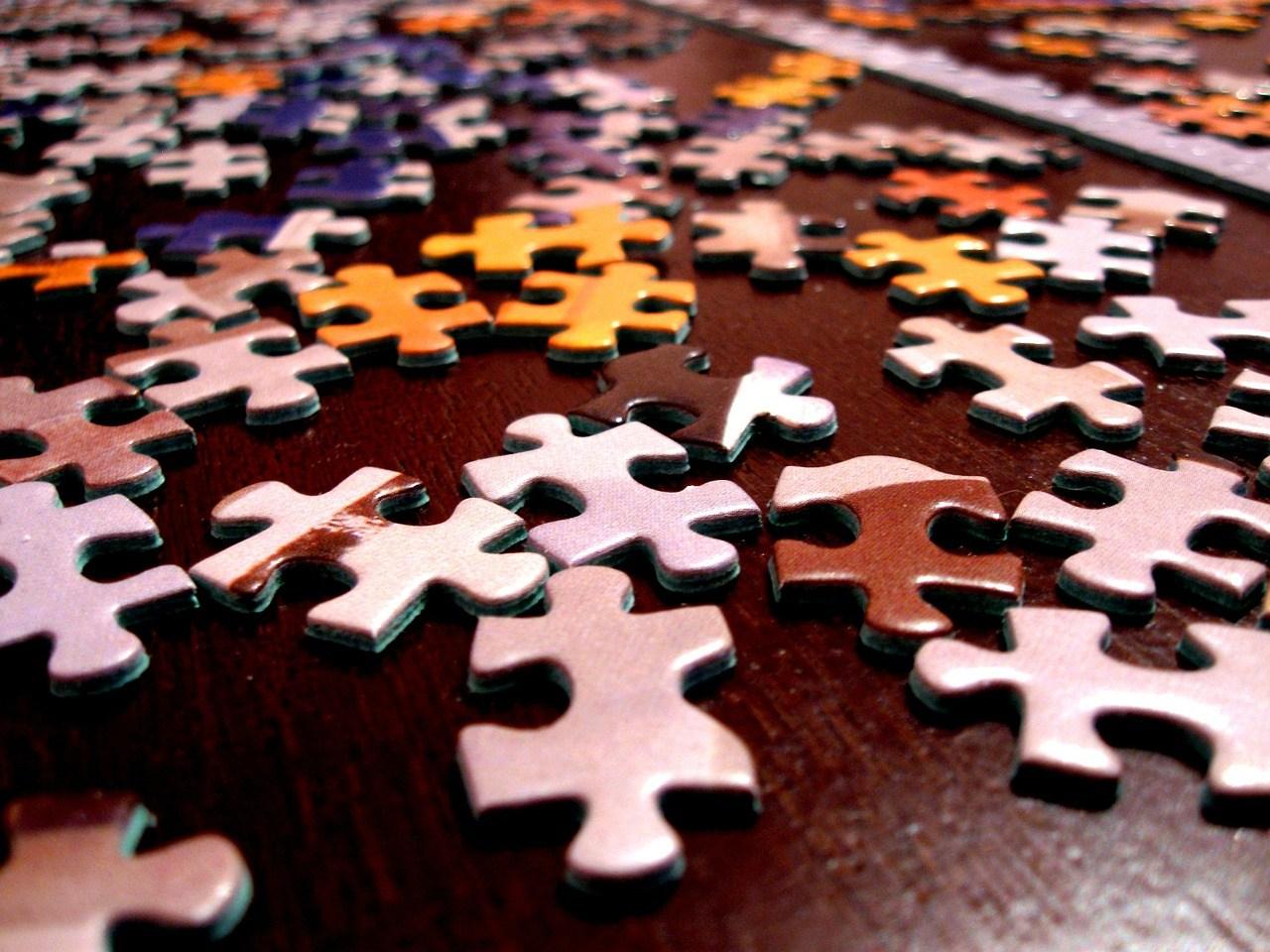
By Pierre-Louis Frouein
Getting serious about supply chain engagement requires us to do more than just set rules and expect suppliers to follow them. It's not enough to just sign agreements and hire third-party inspectors, though that’s a critical element.
There are three big things any company that's serious about ensuring sustainability and social responsibility in the supply chain must do. They involve getting proactive to do as much as possible to anticipate which suppliers warrant special scrutiny, a willingness to work with them individually both as partner and monitor, and getting inside their operations to get a first-hand look at what's going on.
Five years ago my company, Alcatel-Lucent, made the decision to take our supply chain work from a compliance-oriented effort to an action-oriented one. We built programs to help suppliers set individual goals, to provide support and guidance, and to keep everyone accountable.
The result of that effort: In the last five years, we’ve seen a 50 percent increase in supplier sustainability performance.
Throughout the process, we discovered three key components that can help any company to step up its supply chain work. These three components comprise the three building blocks that move supply chain sustainability from concept and good intentions to action: policy, implementation and success measurement.
1. Set clear goals, then perform indisputable assessments
Any company starting to address supply chain sustainability should begin by surveying its suppliers with a state-of-the-art assessment using well-recognized references. We use EcoVadis, which helps to establish which health, safety, environment, ethics and labor policies and programs are in place, and which ones are lacking.
But assessments alone won’t change behavior. Purchasers must work with suppliers to set goals and communicate the importance of meeting those goals. If suppliers think you’re not serious about achieving goals, they won’t take it seriously. Our production suppliers are aware they cannot remain ‘preferred’ and get more business if they do not meet our sustainability expectations.
It’s important to know the limitations of such third-party assessments. They can provide an excellent snapshot of your supply chain, to know which suppliers need the most help, and they can provide a high-level view of the health and well-being of your supply chain. But they also largely focus on policies and systems, which can sometimes be misleading. For example, a company can have a policy limiting the number of hours employees can work per week, but if that policy isn’t enforced, you wouldn’t know without being on the ground.
That's the place to start with suppliers, necessary but far from sufficient and well short of leadership and deep results.
2. Co-create individualized improvement plans and provide support
Measurement, demands and agreements are not enough. You have to follow through and help suppliers meet demands and keep agreements. You have to recognize that the kind of help suppliers need varies, and be willing to give tailored support. This converts concepts to action.
The typical model is mass training programs in which dozens or hundreds of suppliers can be helped at once. We learned early on that one-size-fits-all trainings would not work. Suppliers have varying needs and group trainings leave gaps that go unaddressed: a software company shares few sustainability problems with a metallic parts manufacturer, but we have both in our supply chain. In addition, companies vary in what they address easily, where they struggle, and, sometimes, in what they try to ignore or hide.
You have to see suppliers as individuals and work with them accordingly. We started holding one-on-one calls with suppliers—over 200 in total—in order to build out individualized improvement plans. This is for monitoring, yes, but it's also for identifying how we can help and how suppliers can help each other.
One-on-one consultations may not be the right solution for every company, but when working with high-risk suppliers in developing countries, we found it invaluable to moving the needle. Standing back and making demands would never be enough. So we find out who we should be concerned about, then develop individualized improvement plans, individualized support, and individualized monitoring.
Once the supplier has completed the improvement plan, we do an EcoVadis reassessment to ensure the company now meets our expectations.
3. Take initiative and get to the front lines yourself
Individualized improvement plans, support, and check-in teleconferences are game-changers, but they also have limitations. So, companies have to go on-site to their suppliers and check things out in person. Use outside audits, remote communications, and/or other risk factors as tools to figure out where there are or may be trouble in the supply chain -- especially scrutinizing the greatest threats to health, environment and human rights.
Then go in-person and see what's going on: Is the emergency exit door truly unlocked? Go find out in person. And if it’s not, fix it on the spot. Hold people accountable right then and there, and keep the offending supplier under close supervision. There's no substitute for getting onto the front lines.
In a recent audit, we found out workers in the production area of one supplier did not have appropriate personal protective equipment (gloves, protection glasses, etc). We instructed the supplier to create a list of rules defining what protection should be worn in each workplace, to make that list available for workers to read at the workplaces, and to instruct their staff to properly implement them. And we keep an eye on whether it's happening.
It’s not financially viable to audit every supplier every year. We conduct around 50 on-site audits annually, which means we need to be strategic. We use several key indicators to determine which suppliers will get audited.
- High-risk activities: We’re not likely to audit a consulting firm or software company. We’re going to focus on suppliers with the highest-risk labour, health, safety and environment profiles, like mechanical parts suppliers.
- Location: Suppliers in China are going to get more scrutiny from us than those from, say, Switzerland.
- Business load: We also look at the volume of business we do with a supplier—and focus on the ones we do more business with.
- Assessment results: Once we’ve done EcoVadis assessments, we focus on auditing suppliers with poor scores.
Supply chain sustainability expectations are changing and there’s more pressure on purchasers to take action and support their suppliers, rather than just sign agreements. It’s no longer enough to simply require compliance—purchasers can and should be ready to roll up their shirtsleeves and provide support. It’s the only way we can ensure that health, labour and environmental disasters are a thing of a past.
Image credit: Pixabay
Pierre-Louis Frouein manages sustainability aspects of Alcatel-Lucent’s global procurement group. He has previously been in charge of special environmental projects within the group, and has been active in industry associations concerned with sustainability in supply chains.
TriplePundit has published articles from over 1000 contributors. If you'd like to be a guest author, please get in touch!