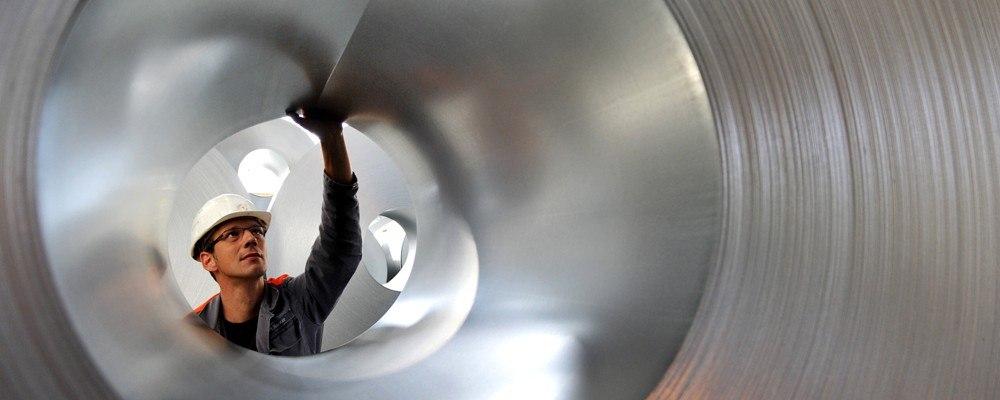
Used widely in nature, lamination – the deposition of fine layers of materials on top of one another – has long been known as a means of manufacturing stronger, more durable and longer lasting metals. Founded in 2006, Seattle's Modumetal is applying the process of lamination at nano-scale, enabling engineers to design and fabricate metals with superior performance characteristics and at lower cost than conventional methods.
The ability to cost-effectively fabricate nanolaminate metals that are more resistant to rust and corrosion alone would be a boon. Such materials could be used by engineering and construction companies for everything from civil engineering of public infrastructure to offshore energy (wind, as well as oil and gas), mining, home and building construction, tools, and consumer products. In a 2002 study, international corrosion authority NACE estimated corrosion in the U.S. results in direct costs of $276 billion a year across the economy.
At present, Modumetal's products fall into one of four lines: structural parts, coatings and claddings, thermal barriers, and armor. Its zinc-based alloy NanoGalv outperforms conventional galvanization processes by over seven times, Modumetal co-founder and CEO Christina Lomasney said during an October 2014 interview for Rigzone. That significantly reduces the need for replacement parts over the life of metal components, as well as the risks and costs of fatigue and failure.
Nano-scale manufacturing of metal laminates
Development, and subsequent acquisition, of a new process to cost-effectively manufacture nanolaminate metal alloys at scale was the pivotal breakthrough achieved by Modumetal's founders.
Rather than employing conventional vapor deposition – expensive and limited in terms of scale – Modumetal essentially “grows” custom-designed metals using an electrochemical process. This results in uniform deposition of nano-scale layers that conform to the exterior and interior contours of any object, no matter how complex its shape or form.
In an October, 2014 interview for Rigzone, Lomasney likened the process to the way Mother Nature builds structural components of living things, such as trees.
“If you look at a tree, you see the theme of a configured material,” Lomasney was quoted as saying. “In Mother Nature’s case, the structure is built so the seasons determine the density of the wood. In our case, electric field modulation is the equivalent of seasons, which is the core technology. We’re basically growing the laminated structure.”
The resulting nanolaminate metals and alloys can be designed to be lighter, stronger, more durable and more flexible than conventional metal products of whatever kind – steel, aluminum, etc. And they can be produced in high volume cost effectively, Modumetal touts.
Nanolaminate metal alloys: Lifecycle costs and commercial prospects
Major offshore oil and gas industry players have shown strong interest in Modumetal's manufacturing process and products. Chevron and ConocoPhillips have invested in the privately-held company.
Modumetal has also announced it's working with Hess on issues including corrosion, wear protection and structural reinforcement.
Building on its commercial prospects in the oil and gas industry, Modumetal in May 2014 announced it commissioned a new production facility in Washington state's Snohomish County. The new facility “is supporting production lines for coatings and claddings of oil and gas production and casing tubulars, and is already expanding to accommodate growing product interest,” management stated in a press release.
Added Lomasney: “By using our patented coating and cladding technology in demanding, highly corrosive and punishing environments, we are demonstrating significant improvements in the performance, durability and longevity of oil-producing assets, all while maintaining cost competitiveness with commodity metal products.”
All other things held constant, effectively extending the life of metal alloys used across economic sectors would mean less demand for these materials and less need to mine more metal ores. Such reductions would also result in less air, water and land pollution by way of mining and metals production, thereby enhancing environmental and socioeconomic sustainability and quality of life.
*Image credits: 1), 2) Modumetal; 2) BillLawrenceOnline
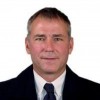
An experienced, independent journalist, editor and researcher, Andrew has crisscrossed the globe while reporting on sustainability, corporate social responsibility, social and environmental entrepreneurship, renewable energy, energy efficiency and clean technology. He studied geology at CU, Boulder, has an MBA in finance from Pace University, and completed a certificate program in international governance for biodiversity at UN University in Japan.