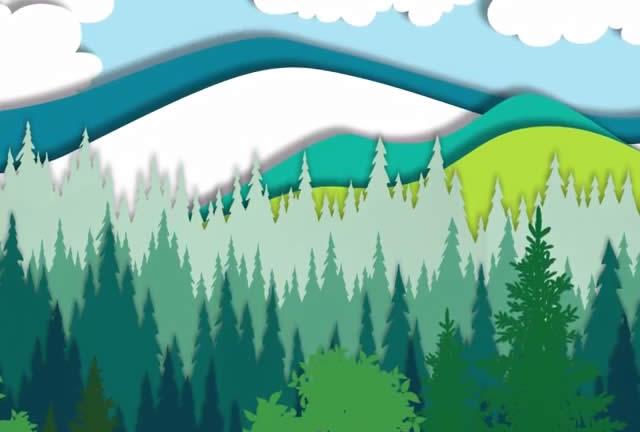
By Elisabeth Comere
Sustainable business strategies seem to be the focus of customer companies today, and companies will continue to move forward with full integration across their supply chains in response to the resource crunch. Here are the top three trends for 2015.
1. Better resource management
Currently companies are facing major barriers to adopting responsible alternatives, like bio-based plastics and FSC-certified fibers, because demand simply isn’t strong enough to put them on a level playing field with conventionally-produced materials. So, how do we raise the bar?
- Establish a Business Code of Conduct for Suppliers (BSfS)
A social and environmental code of conduct will drive responsibility throughout the supply chain by holding each supplier to a higher standard with respect to environmental protection in sourcing, manufacturing, distribution, and the treatment of workers and communities. To be effective, a code of conduct cannot rely on a signature alone as it requires active and regular engagement through data reporting, third-party inspections and audits
- Build upstream partnerships
Engage your base material suppliers by working collaboratively to meet your responsible procurement goals. Working directly with your suppliers is a big opportunity to close identified gaps with a continued focus on driving responsible sourcing.
- Establish a chain of custody
A chain of custody provides transparency from resource extraction to the point of sale. Third-party management and chain of custody certification is more credible than a self-declaration from suppliers as proof that raw materials came from well-managed areas.
- Reporting and evaluating your supply chain
2. Innovative bio-based materials
Multinationals will continue to explore how their operations can contribute to a circular material flow by taking a hard look at the resources entering their supply chains. The premise is to reduce the consumption of primary materials by extending the lifecycle of those in use by reusing, recycling and transitioning to naturally renewable components. More and more businesses will look to responsibly-managed, plant-based sources -- such as timber, sugar cane and dent corn, wheat, biomass wastes, and algae -- to do just that. Renewable material integration moves operations closer to a circular business model; secures a continuous flow of feedstock; and demonstrates a commitment to environmental and social sustainability.
3. Eco-efficient operations
Constantly at play, and often times competing, are two forces: economics and the environment. For Tetra Pak's customers, economic performance is affected by production efficiency, operational cost and total cost of ownership, while action on the sustainability front is largely driven by brand reputation, retailer demands and legal requirements. As we know, these forces can have adverse effects on one another if under-managed or mismanaged, and they need to work in harmony for customers to remain competitive, profitable and sustainable.
We anticipate a growing trend in 2015 of companies using a gate-to-gate approach for reducing the environmental impact of production processes – a holistic methodology that is used to optimize each stage of a product’s lifecycle. At Tetra Pak, we recognize this can seem like a daunting but necessary task for operations, especially for those companies that already have fully established systems in place.
To better help our customers, Tetra Pak has launched a new Environmental Benchmarking Service, a comprehensive audit that is used to measure generated waste, energy and water consumption of the entire processing plant. Based on this audit, the Tetra Pak Technical Service team will then provide specific recommendations on opportunities for improvement, helping customers not only to reduce their environmental impact, but also to lower cost.
Pilot projects have been carried out in the U.S. and in Europe, delivering average costs savings of around 20 percent. For example, at Pacific Foods, a U.S.-based producer of organic foods and beverages, opportunities were found to reduce the company's carbon footprint by approximately 3,500 tons of CO2e and to cut its water consumption by some 31 million liters every year.
Elisabeth Comere is responsible for environment at Tetra Pak – the world leader in packaging and food processing solutions. She joined the company in 2006 as Environment Manager for Europe where she helped define and drive Tetra Pak’s environmental strategy and contributed shaping recycling for cartons in Europe. Since 2010, she is based in the U.S., focusing on advancing the Tetra Pak’s commitment to sustainability in the U.S. and Canada and is involved in various industry and customer packaging and sustainability initiatives.
TriplePundit has published articles from over 1000 contributors. If you'd like to be a guest author, please get in touch!