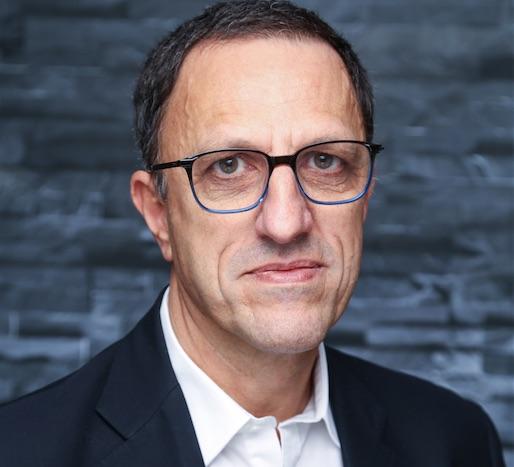
Sustainability. Now that this word is firmly entrenched in the business landscape, the real question is just how committed organizations are to sustainable practices vs. bottom-line results? This is a story of two companies involved in road construction that have sustainability in their DNA, and how they are collaborating to help solve one of the industry’s great conundrums.
Skanska, a leading project development and construction company, espouses a comprehensive sustainability strategy that addresses several areas, including a “green” component that sets environmental goals for all its business units. Skanska Sweden is committed to becoming carbon neutral by 2050, and its policies and practices are oriented to achieving this objective. Meanwhile, Kraton, a global producer of specialty polymers and chemicals, is developing new applications for its bio-based products.
The road construction industry’s priority is to build safe and durable roads for the public. Over the years, the road industry has worked to reduce its end of life product by increasing the amount of asphalt it reclaims from old roads and uses in road maintenance and new infrastructure projects. But to achieve the most value in using reclaimed asphalt (RA), there is a persistent challenge: RA is normally used in the lower layers of roadways, not in the critical surface layer. Why? Surface layer asphalt mixes including more than 30 percent RA tend to be too stiff, resulting in road performance problems such as cracking susceptibility.
To meet the challenge of using high percentages of RA in surface layers with no drop-off in road performance, Kraton spent three years developing a pine chemical additive to treat the RA. This product, SYLVAROAD™ RP1000 Performance Additive, reactivates and mobilizes the binder so it is reinvigorated at the molecular level, rather than simply diluting the material as many petroleum-based additives do. This enables reuse of greater quantities of RA, which minimizes asphalt disposal and reduces the need to manufacture large amounts of new/virgin asphalt. Tests have even shown that up to 100 percent RA can be successfully used on surface layers.
In 2016, seeing promise in the pine-based additive, Skanska used it to pave a section of Swedish Road 694, near the city of Västerås. The mix containing 70 percent RA was applied to the road’s surface layer. In contrast, the norm in Sweden is 20 percent. After a year of use, the road is holding up well to traffic of nearly 3,000 vehicles per day. Now Skanska is using SYLVAROAD RP1000 combined with RA to pave more roads, employing a diligent monitoring process that checks for fatigue, deformation and other issues in the various road layers. In addition to Skanska’s projects, some 50 high-RA plus SYLVAROAD trials with other asphalt makers and road contractors in Europe, Asia and the U.S. are underway.
Enabling the use of more RA in road construction results in other sustainability benefits as well: significant decreases in carbon emissions and reduced construction costs.
As industries worldwide focus on sustainable practices that not only benefit society but are also tied to bottom-line success, it is crucial to extend the life cycle of every resource and product, realizing their full value. The Skanska-Kraton collaboration is a prime example of such stewardship.
Bruno Vuillier is Market Development Manager at Kraton.