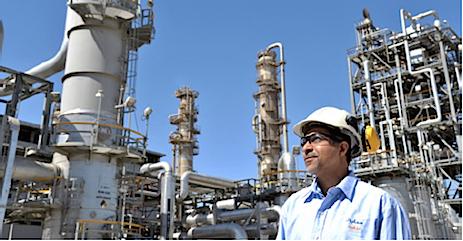
The Saudi Arabian Basic Industries Corporation (SABIC) cuts carbon emissions by recycle CO2. Miranda Ingram reports…
Global petrochemical giant SABIC is celebrating its large-scale circular economy initiative whereby waste CO2 that used to vent into the atmosphere is now being converted into feedstock for the company’s manufacturing facilities. This drastically cuts carbon emissions and reduces the purchase of natural gas. The initiative is both an environmental and a financial triumph.
“SABIC has been a sustainable company since its foundation by turning excess gas into useful products,” said Corporate Sustainability Director Gretchen Govoni, “but our sustainability function began in 2008, when we started examining our energy and water usage and greenhouse-gas emissions. As we collected and analysed our data it became apparent that our biggest opportunity to make a difference was not in cutting traditional hazardous waste but in tackling our carbon emissions.”
SABIC’s dedication to sustainable innovation is ‘Chemistry that Matters'™ to the environment and future generations.
“We committed to reducing our CO2, energy and water usage by 25 percent, and our material losses by a massive 50 percent by 2025, on an intensity basis,” said Govoni. “That was the pledge; the question was, ‘how?’”
With more than 12,060 global patents and applications, SABIC has operations in over 50 countries and a global workforce of over 40,000. A considerable amount of its manufacturing is done in Saudi Arabia in the industrial city of Jubail, which includes several wholly-owned manufacturing affiliates and other joint ventures.
“Our sustainability team was able to collect all the corporate data and see the potential in integrating materials between plants,” Govoni explained.
SABIC’s manufacturing affiliates operate several processes which produce highly concentrated CO2, such as the manufacturing of ethylene glycol and ammonia. The CO2 stream from the ethylene glycol plant contains small quantities of impurities that must be removed to be suitable for reuse.
Step one involved SABIC working with Jubail-based affiliate United, which produces ethylene glycol, to build a CO2 recapture and purification plant, which first dries and compresses the CO2 stream coming from the ethylene glycol plant, then removes the remaining hydrocarbons and other contaminants. What emerged is the world’s largest CO2 purification plant, producing CO2 pure enough not only to use as feedstock but also to sell to the food, beverage and medical industries.
Operational since last year, the CO2 plant at United can purify up to 500,000 metric tons of CO2 from ethylene glycol production annually—roughly the amount produced by powering 70,000 homes for a year.
The second step was the sustainability project which required cross-site collaboration and involved building 25 km of pipeline to deliver the purified stream to nearby affiliates to use in their manufacture of products such as urea, used in fertilisers, methanol, a basic chemical building block used in such things as plastics, fabrics and construction, and 2-ethylhexanol.
“The affiliates were initially cautious,” said Govoni, “but once the financial rewards—reducing natural gas supply costs—were as clear as the environmental advantages, everyone got excited.”
The project increases economic returns, enhances the social value by producing more products from the same amount of raw material, and improves environmental emissions. “It is win-win,” said Govoni.
Moreover, SABIC’s investments in energy and resource improvements have helped reduce operating costs, making SABIC and its affiliates more resilient to market dynamics.
As the affiliates came on board, one of them, SAFCO, launched the SAFCO V plant, which is designed to use 780,000 metric tons of CO2 per year as feedstock to produce urea. This helped increase the overall resource efficiency and CO2 intensity of SABIC’s urea operations. It will have an even greater impact on the company’s greenhouse gas-intensity performance during its first full year of operation in 2016.
Already last year, SABIC greenhouse gas intensity, measured in Metric Tons of CO2 equivalent per MT of product sales, fell 2.6 percent below 2014, and 7.8 percent lower than 2010, their base year.
This leadership in carbon emission reduction was recognised during the Carbon Sequestration Leadership Forum (CSLF) Ministerial Meeting in November 2015 in Riyadh, an international climate change initiative, where this project received a certificate of recognition. The CSLF focuses on the development of improved cost-effective technologies for the separation and capture of CO2, as well as for its transport and long-term safe storage.?
“International recognition highlights SABIC’s contribution to carbon capture and utilisation and our commitment to building value for all the dimensions of sustainability to create ‘Chemistry that Matters™’,” said Govoni. “The initiative is also a good example of how a large integrated complex of affiliated operating sites can collaborate to reduce overall CO2 emissions.”
While this is good for SABIC’s corporate reputation, the award, along with the sheer scale of the initiative, also prompted a feel-good factor among the company’s employees. “For many years we have been making small sustainability improvements, setting short-term savings goals,” Govoni said. “This innovation is so large and involved so many people that it has generated huge excitement around the circular economy amongst our staff. Now, they get the big picture and understand not just the environmental good of sustainable practices but their economic viability, too.”
“Looking to the future, we will continue to look for ways to improve resource efficiency by sharing energy or materials between sites,” she said. “And our?technology and innovation teams worldwide are also looking into additional ways of converting CO2 into valuable products.”
United is already selling its purified CO2 off-site and now, there is interesting research into developing a catalyst that converts CO2 into alcohol during the natural gas reforming process.
SABIC is also in the midst of a multi-year effort to upgrade catalysts in ethylene glycol processes to lower CO2 byproduct and further reduce overall greenhouse gas emissions. There are two projects within the United Nations Clean Development Mechanism (CDM) program: The Al-Bayroni project in Jubail was registered in 2014, and the UN audit for a project in a second affiliate is scheduled to be completed in 2016. These two projects are expected to save another 600,000 MT of CO2 eq in their lifetimes.
TriplePundit has published articles from over 1000 contributors. If you'd like to be a guest author, please get in touch!