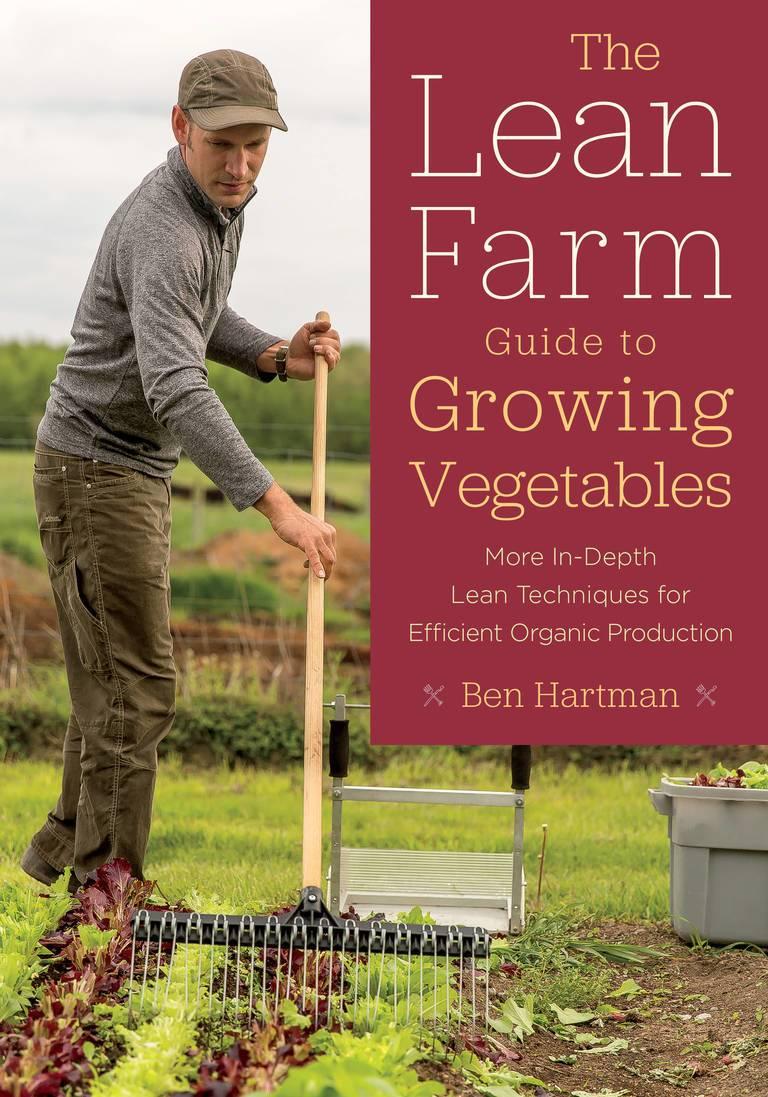
By Ben Hartman
This article is adapted from Hartman’s book The Lean Farm Guide to Growing Vegetables (Chelsea Green, 2017) and is excerpted with permission from the publisher.
In 2011 I received an email from Steve Brenneman, a CSA customer and the owner of an aluminum trailer factory. He had recently transformed his factory using the lean system, a Japanese invention designed to cut out waste and increase profits with less work. Brenneman offered to help my wife and I do the same on our farm. After initial skepticism (factory methods on farms haven’t always churned out sustainable outcomes), we took him up on his offer. Over the following several seasons, we proceeded to declutter our workspaces and cut waste from our processes. We now earn a comfortable living from our farm, and neither of us works off the property. We have stable, long-term customers, and our work doesn’t overburden us. The following are the five core lean business principles that have benefited us the most.
1. Keep only the tools that add value
Lean relies on an organization method called 5S for keeping workspaces clean. The most important step is seiri (sorting), or discarding any item from your workspace that is not used every season to create value. This has not always been easy for us to do. At first we placed too much stock in tools that, realistically, we would never use. Now we have routines for constantly making sure we are surrounded only by what we need.
Farmers love to collect tools and hoard things. But we must check that instinct because everything we keep has a cost. It costs time to trip over shovels and look for hoes. It costs to store items—property taxes on buildings and expenses to maintain those buildings. Plus there is the mental cost of living with clutter. These are costs that suck energy and money without giving anything back besides the vacuous satisfaction of ownership.
2. Let the customer define value
A second practice underlying our daily work is to always have our customers and their wishes in mind. We are growing food for them, and the products they want, both goods and services, guide our work. Specifically, we seek out answers to these three questions:
- What do our customers want?
- When do they want it?
- What amount do they want?
The more precisely we answer these questions and deliver on the answers, the more profitable we will be at year’s end. To be sure, we don’t fulfill every wish. For example, while customers might love watermelons, we don’t grow them because, for us, they are not profitable. Still, continually posing and answering the three questions ensures that paying customers, not our own whims, steer our farming.
3. Identify the steps that add value
The next principle we follow is to carefully trace value. In which steps do tomatoes and peppers and carrots become more valuable? When are we adding to their value, and when are we just spinning wheels? In a factory setting, value might be added when steel is welded to steel. That is the point when each piece is suddenly worth more. On the farm we’ve found that surprisingly few actions—seeding, harvesting, and washing food, for example—build value. These direct actions cause our food to be worth more.
4. Cut out the muda—anything that does not add value
According to the lean system, actions on your farm that don’t directly add value—like lawn mowing, cleaning, and leafing through catalogs—are considered muda.
On our farm we take muda elimination seriously. We look for the 10 mudas all the time. When we see them, as much as possible, we get rid of them. While muda is usually translated as “waste,” not all mudas are completely superfluous. We still file taxes, occasionally pull weeds, and send invoices to customers, even if these actions do not directly cause our products to be worth more. Not all mudas should be completely eliminated. The goal, rather, is to minimize the amount of time and energy given to non-value-adding activities.
We’ve come to realize that every activity we perform is either muda or value adding. There are no exceptions. Our job is to see the difference, and steer toward value. If we find ourselves performing a muda task, we ask, how can we shorten it or, better yet, eliminate it? As Shigeo Shingo, a Japanese engineer and arguably the world’s leading expert on manufacturing efficiency, observed, only the last turn of a bolt tightens it—the rest is just movement. We want to focus on bolt tightening, so to speak—on seeding, washing, harvesting, and selling—and minimize everything else. Cutting out muda has been a powerful force on our farm, increasing our profits every year, while we work less.
5. Practice kaizen—continuous improvement
The final step is to practice kaizen, or continuous improvement, rooting out more waste every year from the farm, and aligning production more tightly with customer demand. We have adopted the philosophy “When you fix it, fix it again.” Our goal is to create a farm culture where everyone on the team joins together in an effort to achieve zero-waste production.
The end goal of the five steps is compression. We want to shorten the timeline from beginning to end, from the idea to grow a crop to the moment we receive cash. Along the way our production area shrank from 5 acres to less than 1, and we shed thousands of pounds in tools and supplies. We started farming because we loved working with plants. Lean has not stripped the joy from our work. It has given us focus so that with fewer distractions—less muda—we enjoy our work now more than ever.
Ben Hartman is also the author of The Lean Farm (Chelsea Green, 2015) and has been named one of the top 50 emerging green leaders in the United States by Grist on their list of innovators with fresh, forward-thinking solutions to some of humanity's biggest challenges. Inspired by Toyota’s “lean” approach to manufacturing—a production strategy aimed at minimizing waste and maximizing efficiency—Hartman has become an expert in applying these business principles to his small produce farm in northern Indiana making it more environmentally and economically sustainable.
Farm image: David Johnson Photography
Book cover image: Chelsea Green Publishing
TriplePundit has published articles from over 1000 contributors. If you'd like to be a guest author, please get in touch!