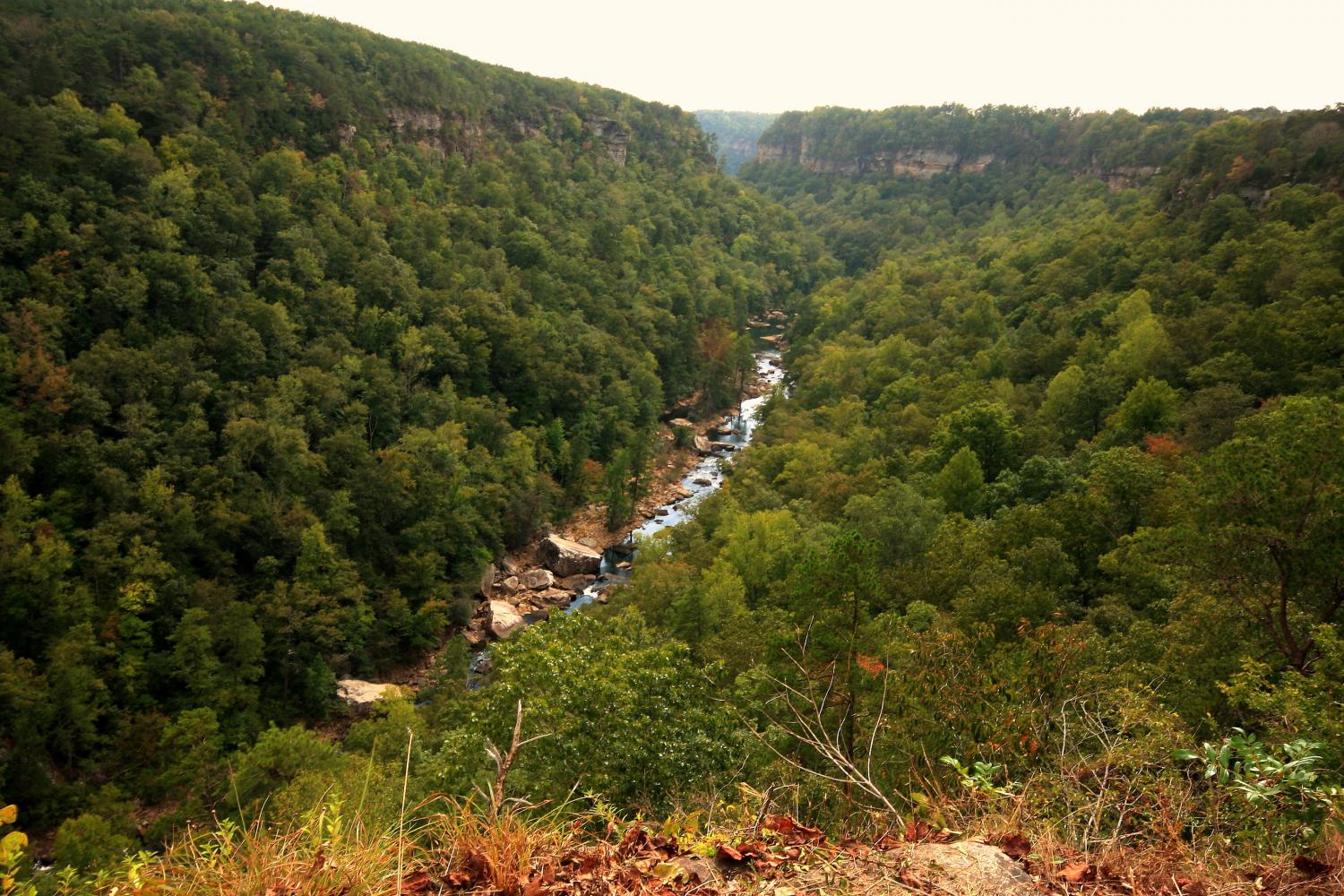
Rural America, with its large-scale agriculture and natural-resource converting mills, has long been at the forefront of automation - but 21st-century challenges are mounting, from Alabama to West Virginia.
Think about a job in rural America. What do you imagine? A farmer seated at the wheel of his John Deere? A logger, in hardhat, headed to the woods with a chainsaw?
What if I told you that the John Deere tractor was largely self-driving thanks to a GPS system developed in part with NASA’s Jet Propulsion Laboratory? Or that instead of a chainsaw, the logger is seated at the helm of a tree-felling machine that requires skill akin to piloting an airplane?
Rural America, with its large-scale agriculture and natural-resource converting mills, has long been at the forefront of automation. While driverless cars are regularly making the news now, driverless tractors have been in use for 15 years and mills rely on precise computer-driven equipment to turn raw wood into a variety of goods with minimal waste. These rural businesses largely churn out commodity-based products, meaning that a slight edge in production speed and output could make a huge difference in the success or failure of a business, particularly in a global market. For many rural businesses, the question of survival is simple, embrace technology or die. The answer, however, is not always as easy and requires access to flexible and favorable capital to make the large expenditures of implementation possible.
Making “working the mountains” safer
In West Virginia, loggers have worked the woods for decades with chainsaws, bulldozers, and woods tractors called “skidders.” On the steep hillsides of the Appalachian Mountains, this means little protection for workers from falling or sliding trees, making it no surprise that the Bureau of Labor Statistics identified logging as the civilian occupation with the highest rate of fatal work injuries in 2015. It also contributes to logging’s reputation as a dangerous and difficult job and limits the industry’s ability to attract new or younger employees.
The Lyme Timber Company LP, a timber management organization with a track record of sustainable management, is working with its logging contractors to bring winch-assist, or tethered logging, technology to Appalachia. With this technology, which is new to the Eastern US, enclosed cab machines that mechanically harvest trees are tethered by cables to an anchor machine at the top of the slope. This provides support for the harvesting machine to remain upright on the hill and protects workers within the cab. A traditional, hand-felling logger might earn $15-18 per hour for a high-risk job, but the logger at the helm of a winch-assisted felling machine has extensive training, greatly reducing his or her risk of injury, and can earn substantially higher wages.
This technology, however, comes at a cost. A single harvesting operation requires a capital investment of $3 to $4 million and productivity with the system requires several months of training. Costs are typically borne by the logging contractors, who can find it challenging to secure equipment financing loans due to variable income streams and lack of personal collateral to serve as a loan guarantee. Lyme has committed to help its contractors access this technology by providing long-term contracts that offer the contractors a reliable income stream and paying for equipment training. To catalyze investments in this technology and demonstrate their potential for safety, productivity and higher wages, Lyme may capitalize a locally managed logging business. Lyme has been able to make these commitments thanks to the financial flexibility provided to the company through the receipt of an investment via the New Markets Tax Credit program, a federal program that incentivizes private investment in businesses located in or serving low-income communities.
Exploring new industries
Alabama has the second largest commercial timberland base in the U.S., with 23 million acres, and the forest products industry has historically played a major role in the state’s economy.
Yet a decade ago, as housing starts stalled in the wake of the 2008 recession and global competition increased, Alabama’s forestry resources were underutilized. So the idea that The Westervelt Company would develop a wood-pellet plant in central Alabama had everything going for it: a product designed for export, a location suited for easy transportation of local feedstock and finished goods, and a population that wanted to work, but was lacking in opportunities.
The pieces were all in place, but even with significant developer equity and bond financing by the state, The Westervelt Company couldn’t complete the capital stack necessary to afford the purchase and installation of the high-tech equipment needed for the plant. An investment incentivized by the New Markets Tax Credit program was the necessary catalyst to transition Westervelt’s plan from a good idea to a local economic driver that created at least 30 high-quality jobs at the factory, and supports a similar number of wood harvesters, truckers, and barge operators along the supply chain.
As Brian Luoma, President and CEO of The Westervelt Company said “We were excited about bringing a pellet plant to this region of the state, and our recent joint venture with Pinnacle Renewable Holdings reinforces our commitment there. Between Pinnacle’s industry expertise and our supply chain advantages, this plant has the potential to be a leader in the pellet industry and an important part of this community for years to come.”
Jordan Billups, a Team Leader at Westervelt Pellets explains, “I was born and raised here and can speak from firsthand experiences that the plant in Aliceville offers great employment opportunities for the community. Through my more than five years here, I have had the chance to grow, develop, and gain knowledge as a leader.”
The new rural job
Much has been said about how automation and technology has resulted in a reduction in the quantity of jobs in rural communities. However, much less attention has been paid to the fact that these same technologies, as demonstrated by Westervelt and Lyme Timber, have increased the quality of the jobs available (and in both companies’ cases, increased the overall number of jobs as well). The trend of technology enhancement is here to stay and, provided programs like New Market Tax Credits continue to make those technologies financially attainable, the result is clear: the future of rural jobs will not only be more productive on a per-capita basis, but will be higher-skilled, higher-paying, and safer. A win for rural businesses and workers.
Image credit: Evangelio Gonzalez/Flickr
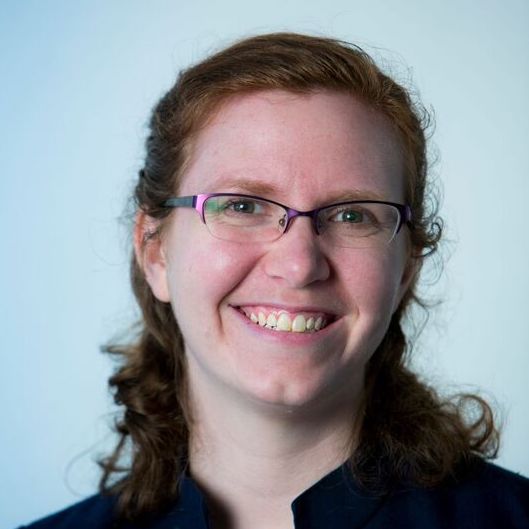
Leah B. Thibault is Director of Executive Administration & Special Projects at CEI Capital Management which creates and preserves jobs and improves quality of life in rural, low income communities by providing access to project capital through New Markets Tax Credits. It is a subsidiary of Coastal Enterprises (CEI). CEI integrates financing, business and industry expertise, and policy solutions to increase good jobs, advance environmentally sustainable enterprises, and grow more broadly shared prosperity in Maine and other rural regions. CEI is committed to building an economy that works for everyone, particularly people with low incomes, women, minorities and people of color. Learn more at www.ceimaine.org.