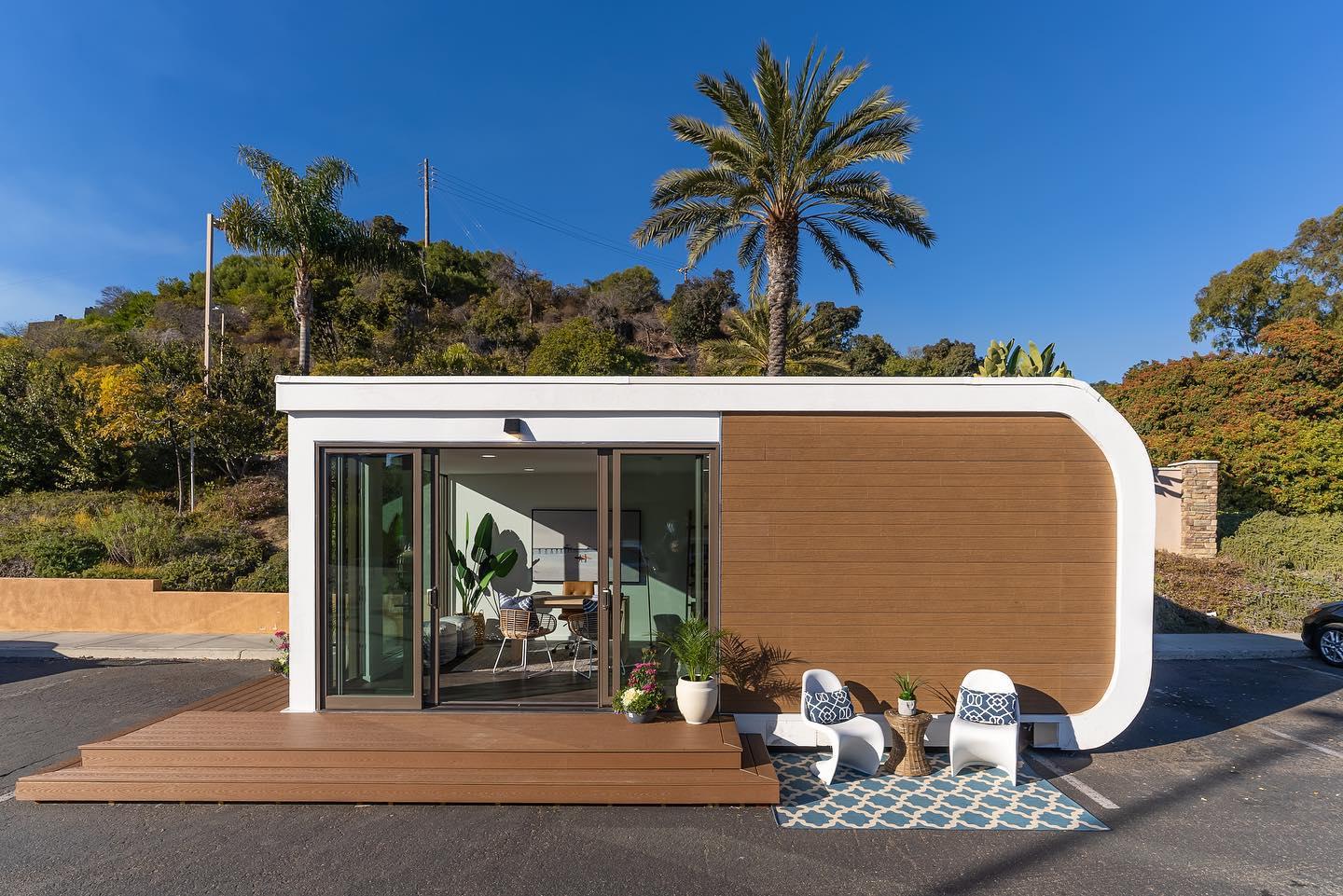
The U.S. and California, in particular, are in the midst of a housing crisis. According to Freddie Mac, the U.S. housing market is short 3.8 million homes. A lack of affordable housing primarily fuels the housing shortage. As construction costs increase, homeownership is an elusive goal to many. Could more sustainable building practices, such as the scaling up of 3D prefab homes, help?
Although there have been considerable advances in green building practices, often, these innovations are not adopted by developers. Meanwhile, climate change is causing flooding, sea-level rise, severe storms, and wildfires, and housing needs to be resilient to these forces.
Concern for the environment and humanity inspired the creation of the 3D prefab homes builder Mighty Buildings. The company embraces robotics, 3D printing and automation to create modular homes in California. Mighty Buildings can print a floor, walls and ceiling in 24 hours while dramatically reducing the waste associated with new builds.
“The housing crisis is big enough that there is no one solution,” says Sam Ruben, Chief Sustainability Officer and co-founder of Mighty Buildings, in an interview with TriplePundit. “We’re talking about needing billions of homes globally. Our vision is to be a tool for industry, mitigating the climate impacts of that additional housing.”
Why consider 3D prefab homes?
Traditional home construction generates three to five pounds of waste per square foot. One of the most impressive benefits of Mighty Building’s 3D prefab homes is the cutting of its construction waste by 95 percent. This is a staggering figure considering between 25 and 40 percent of the U.S. solid waste stream is related to the construction industry; only a small sliver of it is recycled.
Mighty Buildings has the big picture in mind and has been working with developers, planners and building departments from the start to understand their needs and concerns. “We believe in disruption through collaboration,” explains Ruben. “We’re excited about learning as we develop our technology. We have been working with UL, who is a global leader and has 100 years of experience. They are uniquely situated to understand our technology.” In fact, Mighty Buildings became the first such company to be certified to UL 3401 for 3D printing in construction.
All of Mighty Building’s models range between 350 and 1,440 square feet, but they plan to move into townhouses and the multifamily housing market soon. The smaller models work incredibly well with urban infill initiatives that reduce sprawl and conserve land. Smaller homes also require fewer resources to heat, cool, and furnish, promoting affordability.
The average new home size in the United States has fallen since 2016. Ruben finds there is pent-up demand for smaller homes in California and believes it is vital to offer right-sized homes. Mighty Buildings produces a line of Accessory Dwelling Units (ADUs) as a secondary house, office, apartment or in-law unit. The line of single-family homes features two to three bedrooms and range from 864 to 1,440 square feet.
Efficient, agile and safe
Mighty Buildings has transformed numerous aspects of its operations to remove many inefficiencies that plague the construction industry. In most homes, a variety of tradespeople must work on the house, often creating scheduling issues. There is also a shortage of skilled builders in many markets, fueling long delays.
By contrast, Mighty Building’s panelized structures are compliant with California building codes and are fire-resistant. The 3D prefab homes are constructed in the company’s Oakland, California, factory using robotics and digitization. Creating houses in the factory allows for precision and quality control that isn’t possible on a traditional building site. This streamlines the construction and permitting process, dramatically cuts labor hours and the time it takes to acquire a new home. The modular homes are then delivered using a truck and put into place by crane.
Assisted by $70 million in venture capital, Mighty Buildings plans to expand its factory capacity and construct 300 homes next year (growing to 1,000 per year in the future). The houses are suitable for various building sites and are made of a non-silicate light stone material and steel components. This home composition presents an excellent opportunity to innovate and move towards a circular design, says Ruben.
“We’re looking at improved formulation by reducing the polymer that is used, having more recycled content, and using new technology like chemical recycling of ingredients to create a circular opportunity. And, the chemical industry is kicking into gear in understanding what it means to be sustainable. Fiber reinforcement helps with dematerialization and allows us to move into producing multifamily housing and reducing the use of steel.”
A bold, climate-neutral future
The company has conducted a life cycle assessment and has set a goal to be carbon neutrality by 2028 while minimizing the use of carbon offsets. Mighty Buildings also has an internal goal to be carbon negative by 2040 by having regenerative practices that reduce carbon in the atmosphere.
Mighty Buildings eventually wants to turn its attention to deep energy retrofits of existing building stock by installing 3D printed panels that attach the outside of the home, creating minimal disturbance to inhabitants.
Ruben believes it is essential to solve the housing crisis in a way that doesn’t exacerbate the climate crisis. He also believes that homes need to be created with sustainability in mind from the beginning. Furthermore, building net-zero energy homes also takes the pressure off of power plants, some of which are coal-fired.
“It’s a dual crisis,” says Ruben. “The climate crisis has a significant impact on housing stock due to wildfires, floods, rising sea level. It is essential to have resilient housing.”
Image credit: Mighty Buildings/Facebook
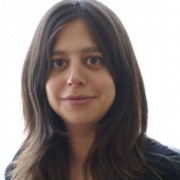
Sarah Lozanova is an environmental journalist and copywriter and has worked as a consultant to help large corporations become more sustainable. She is the author of Humane Home: Easy Steps for Sustainable & Green Living, and her renewable energy experience includes residential and commercial solar energy installations. She teaches green business classes to graduate students at Unity College and holds an MBA in sustainable management from the Presidio Graduate School.